Insulating refractory shapes and straight bricks
Our portfolio of refractory materials
We produce lightweight insulation fire bricks with densities ranging from 400 to 1300 kg/m3.
Our portfolio includes insulating fire bricks and shapes with a temperature classification from 500 °C to 1400 °C. They use high-quality European chamotte and high-alumina raw materials with good thermal insulation.
The bricks are manufactured from dry masses on a press, allowing us to give our products almost any desired shape. Our bricks are available in rectangular form and as wedges, tiles, shapes, and large-size formats.
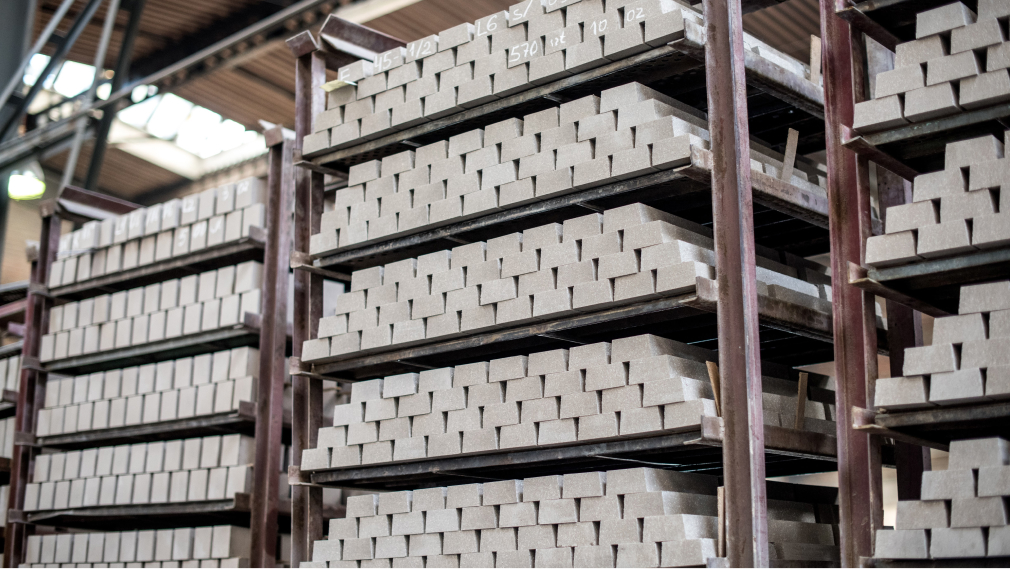
Our products
Fired insulating bricks
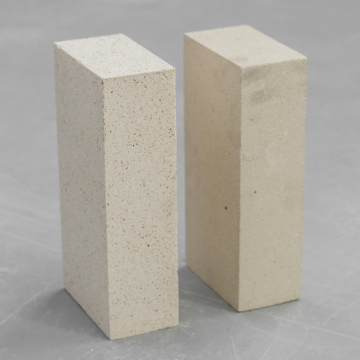
Compared to the most commonly available imported lightweight insulating fire bricks from Asia, our insulating bricks stand out for their higher strength and resistance to mechanical factors. We achieve high resistance by using local raw materials and applying a production method based on pressing. In the production process, we do not use burnable pore-forming additives, which allows us to avoid additional emissions of harmful gases.
Isolux
Ask for technical documentsThe ISOLUX product line includes our insulating bricks for high-temperature industrial applications, which have a wide range of temperatures from 500 °C to 1400 °C. Despite their low densities, these products feature high compressive strength, up to 21 N/mm². They are intended for use in the insulating layer of furnace linings.
Perlite insulating firebricks
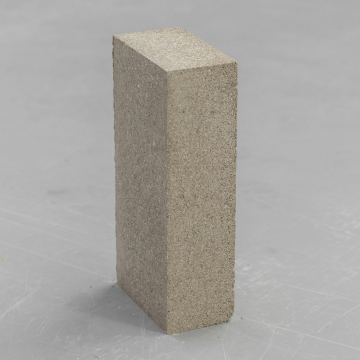
Our lightweight, unburned perlite-insulating fire bricks offer excellent insulation. They are recommended for use in temperature ranges from 400 °C to 1000 °C, enabling significant energy savings. They are available in standard rectangular formats.
Perlitex
Ask for technical documentsIn the PERLITEX line, we offer insulating bricks produced by forming and air-binding methods - without firing. This process yields a product with excellent thermal conductivity and very low density. Their typical recommended application is as the second layer of insulation in ceramic masonry.
Shapes
We can shape ceramics in any way
In the refractory lining design, flexibility and the ability to adapt the lining's shape to the specific shell and installation conditions play crucial roles. Thanks to our versatile molding department, large series reaching thousands of pieces and short runs, including a few pieces of complex ceramic shapes, pose no challenge for us.
We are involved in both the design and production of all necessary molds. For each shape, we prepare a detailed execution drawing. Over more than 170 years of activity, our specialists have developed documentation and a parts database, enabling the execution of over 35,000 shapes on demand without producing new elements.
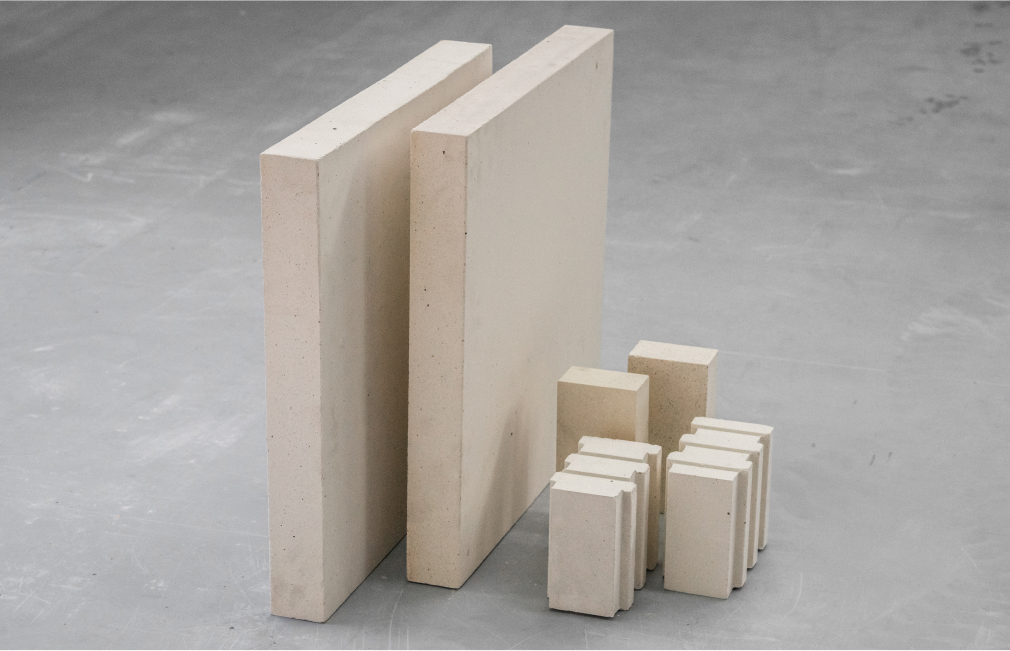
Why choose our products
Predictable and consistent product quality
Thanks to the multi-point quality control plan, we can ensure that each batch of delivered products complies with the established tolerance limits, regardless of the shape of the product and the size of the batch.
Polish-made insulating brick
Our insulating products are manufactured at our single facility in Poland, allowing us to offer shorter delivery times compared to the most popular insulating bricks imported from Asia on the market.
High mechanical strength of products
Compared to typical insulating products available on the market, which are relatively light and brittle, our insulating brick stands out for its significantly higher mechanical strength. This strength is even three times greater than comparable insulating bricks from Asia. As a result, our products are easier to install and provide excellent stability for the insulating layer.
Dry press method production
We manufacture our insulating products similarly to dense-structure products. We form them on a press and then fire them to obtain the final shape. This method allows us to supply standard rectangular formats, such as planting wedges and complex shapes that enable quick bricklaying in heating furnaces.
High packaging standard
We deliver our insulating products to over 40 countries across different continents. We make every effort to ensure that our products reach our customers in the same condition as they left the production line. Well-designed packaging ensures a stable bulk, allowing for the safe storage of pallets even on several levels at the customer's site.
Reliable raw material sources
In our production, we use both primary and secondary raw materials. Primary raw materials are exclusively obtained from certified and vetted suppliers and manufacturers from various corners of the globe. We generate secondary raw materials through the recycling of products and semi-finished products. Each raw material undergoes double quality control - the supplier provides the first and the second, and we conduct ourselves after delivery.
Production process and quality control steps
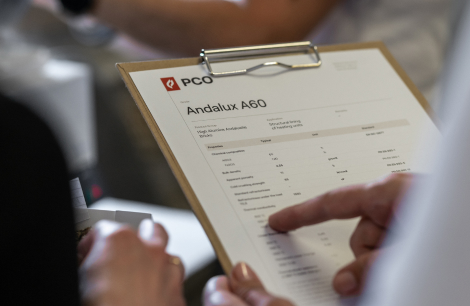
We control the quality of every delivered batch
Quality tests of each production batch are conducted in our fully equipped laboratory. These include checks of chemical composition, density, porosity, temperature resistance, expansibility, and thermal conductivity, which ensures the consistently high quality of our products.
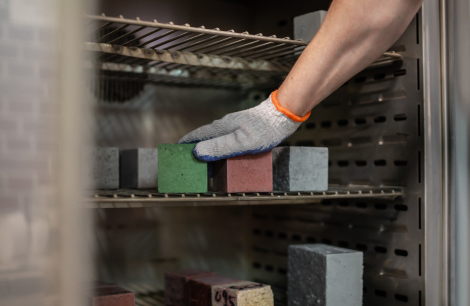
Transparent technical specification of products
Our Technical Data Sheets include a column with the product’s guaranteed properties. A dedicated Standard Tolerances document applies for each family of formed refractory products, clearly defining the quality framework without surprises.
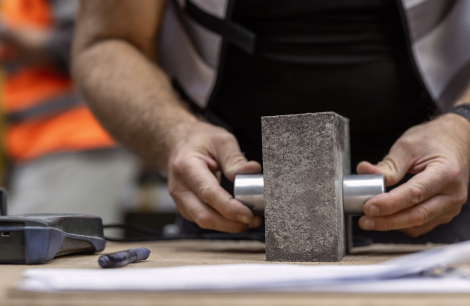
We issue international inspection certificates
We test and report product values according to commonly used industry standards, such as ISO and ASTM. Each order is documented with a type 3.1 certificate by the EN 10204 standard, available in selected languages.
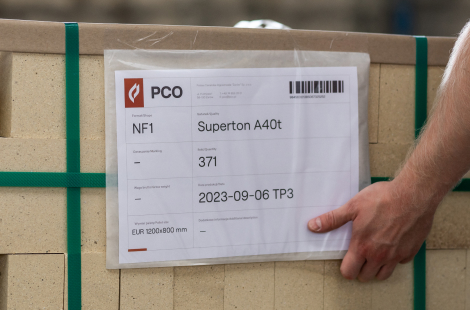
Insight into the production history of each product
All processes in our factory comply with the ISO 9001 management standard. An integrated ERP and workflow management system records every stage of production. Using barcodes, we have complete insight into each product’s history, enabling precise tracking of when and from which batch of raw material was produced.
Supplementary products
In addition to refractory ceramics for the working layer of linings, we also provide a range of additional products.
Do you need help deciding which material to choose or how to arrange the brick layers? Our engineers will perform a temperature flow calculation for you and suggest a layout from the working layer to the insulation layer.
Refractory mortars heatseting and airsetting, ready to use
Ceramic papers, thicknesses 1 to 5 mm
Bulk ceramic fiber, ropes and sealing joints
Semi dense insulating boards, thicknesses 10 to 100 mm
Calcium-Silicate boards
Ceramic fiber blankets, thicknesses 13 to 100 mm
Our offer
Contact us
Please select the option that best describes the subject you want to discuss with us. This will help us direct your inquiry to the right person at PCO.