Refractory shapes and straight bricks
Our portfolio of refractory materials
We specialize in producing refractory bricks and shapes characterized by their resistance to high temperatures up to 1700 °C.
Our product portfolio includes various grades with alumina (Al2O3) content ranging from 20% to 95%, made from materials such as chamotte, andalusite, mullite, bauxite, corundum, and SiC.
We design and produce our mold elements, which allows us to give refractory products almost any desired shape. Over more than 170 years of activity as a manufacturer of fire-resistant materials, we have accumulated a stock of molds that enables the production of over 35,000 different shapes of refractory bricks.
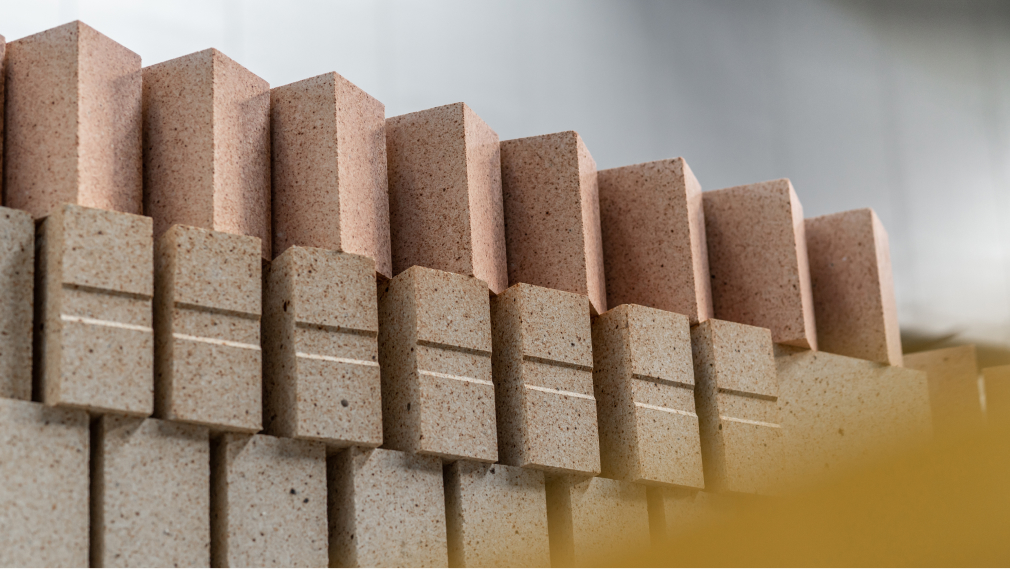
Our products
Fireclay bricks
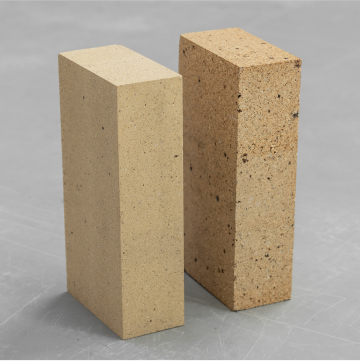
We produce chamotte products using refractory clays as a binding material and fired chamotte, often referred to simply as chamotte. Our chamotte products' alumina (Al2O3) content ranges from 30% to 45%. The temperature range for possible applications can reach up to 1450 °C.
Normaton
Ask for technical documentsThe NORMATON line represents our standard chamotte products. They are suitable for any refractory lining under moderate working conditions, up to 1350 °C.
Superton
Ask for technical documentsThe SUPERTON line consists of multi-chamotte bricks dedicated for applications at temperatures up to 1400 °C. These bricks feature a reduced iron oxide content (below 2%).
Extraton
Ask for technical documentsIn the EXTRATON product line, we've gathered chamotte and multi-chamotte bricks enriched with additives that increase resistance to harsh working conditions, such as abrasion, thermal shock, or chemical corrosion.
Sitonex
Ask for technical documentsSITONEX products are dedicated primarily to applications in coke battery linings. They are characterized by significantly reduced susceptibility to dimensional changes under thermal load. As a result, the lining achieves higher tightness.
Kormax
Ask for technical documentsKORMAX cordierite-chamotte bricks were developed by us to provide a chamotte product with increased resistance to sudden changes in working temperature, known as thermal shocks. They are especially suitable for use in furnace cars.
The ABRAL product line includes kiln bricks with silicon carbide (SiC) based on raw materials from chamotte and andalusite. They are characterized by increased resistance to abrasion and corrosion (alkali influence).
Andalusite bricks
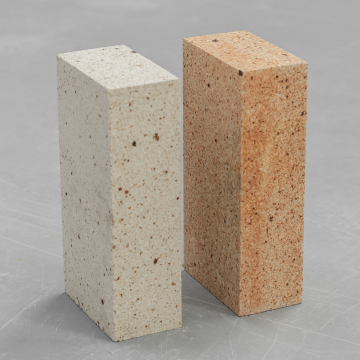
We manufacture andalusite (sillimanite) products from natural raw materials belonging to the sillimanite group, which includes sillimanite, andalusite, and kyanite, as well as high-quality refractory clay. Due to their high mullite phase content, these products are characterized by their high refractoriness under load, resistance to creep at high temperatures, and thermal shock resistance. Sillimanite products are available in several variants: fired, chemically bonded fired, and chemically bonded tempered.
Andalux
Ask for technical documentsThe ANDALUX product line offers a variety of andalusite brick options. In addition to the most commonly provided brick with a 60% Al2O3 content, we also produce products with enhanced strength parameters.
The ABRAL product line consists of silicon carbide bricks based on raw materials from chamotte and andalusite. They are characterized by increased resistance to wear and corrosion (alkali influence).
Bauxite bricks
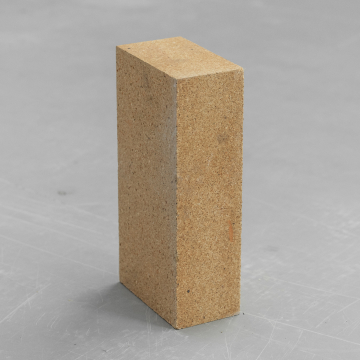
These products are manufactured from calcined bauxites, high-quality refractory clays, and a series of additives that shape the final properties of the product. They represent a group of products with various applications in various industries. They are characterized by excellent mechanical properties and high resistance to thermal shocks, and they also show good resistance to multiple types of slag. Bauxite products come in several variants: fired, chemically bonded, and chemically bonded tempered.
Bauxitex
Ask for technical documentsIn the BAUXITEX product line, we have gathered typical bauxite bricks and product variants with additives that enhance their mechanical and thermal strength.
Mullite bricks
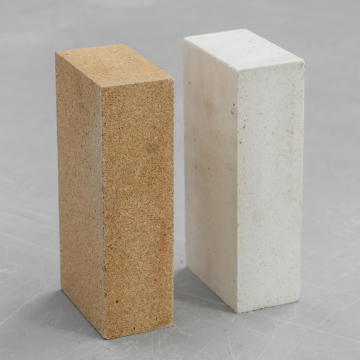
We produce high-alumina mullite products using special refractory clays as a binding material and high-alumina grogs obtained from technical alumina and raw refractory clay or kaolin. For production, we use both sintered and fused mullite aggregates. Due to their exceptional properties, these products have found wide applications in many thermal devices operating in the temperature range from 1400 to 1600 °C.
Mulitex
Ask for technical documentsThe MULITEX line includes typical mullite fire bricks and products based on fused mullite. Products from this line are manufactured using pure raw materials, which results in low porosity.
Alutex
Ask for technical documentsProducts from the ALUTEX line are dedicated to applications in siphon systems used in metallurgy and steel casting. They are distinguished by low porosity and low water absorption.
Corundum bricks
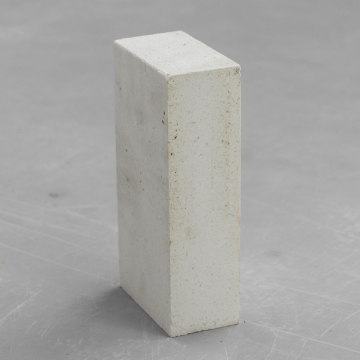
We primarily manufacture corundum products from synthetic alumina, especially fused alumina or tabular oxides. The main phases present in the product are corundum and mullite, which gives these products excellent thermomechanical properties and very high chemical resistance.
Coralex
Ask for technical documentsCORALEX fire bricks have the highest alumina content in our portfolio—up to 95%. They are dedicated to applications at temperatures up to 1700 °C and in the most challenging working conditions of the lining.
Silicon-Carbide bricks (SiC)
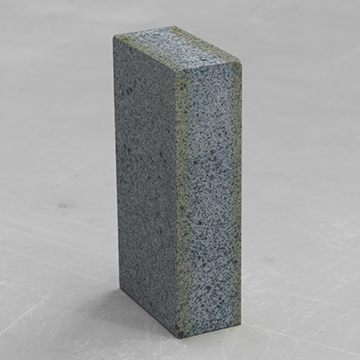
We produce silicon carbide (SiC) products from high-purity synthetic raw materials, mainly silicon carbides and high-purity refractory clay. These products feature unique properties, such as mechanical strength at high and low temperatures and high thermal conductivity. Additionally, they are characterized by resistance to thermal shocks, abrasion, corrosion, and the effects of non-oxidizing slag and metal.
Sicalux
Ask for technical documentsIn the SICALUX product line, we offer SiC bricks based on a ceramic bond. These products exhibit high thermal conductivity and have a characteristic graphite color.
Acid-resistant bricks
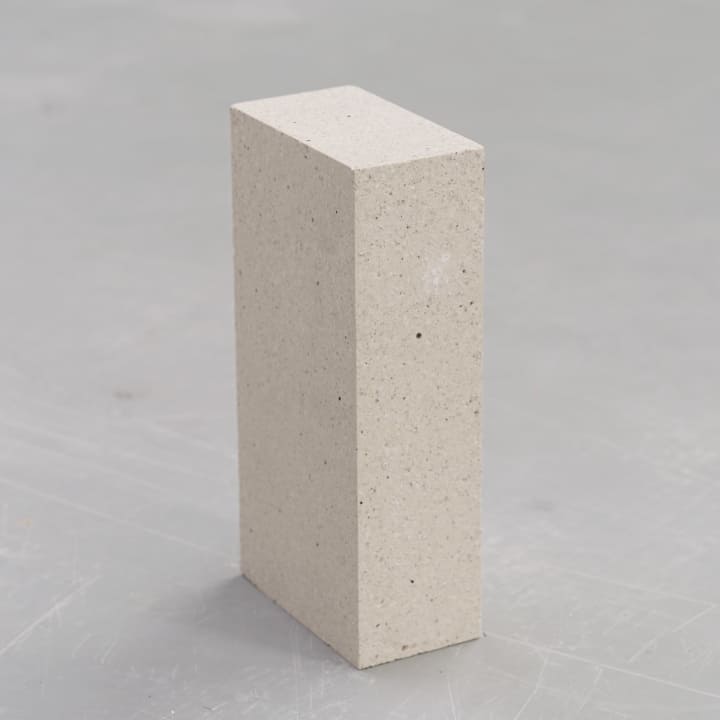
Acid-resistant chamotte bricks are a special type of refractory ceramics primarily used in the lining of furnaces requiring high resistance to chemical substances, including acids. They are made from a mixture of refractory clays (chamotte) and additional components that reduce the product's porosity and increase its chemical resistance. Acid-resistant bricks produced by PCO Żarów contain up to 35% alumina and show solubility in acid not exceeding 2.5% of the product's mass loss.
Resimax
Ask for technical documentsThe RESIMAX line includes our acid-resistant bricks. These products are characterized by low susceptibility to erosion during sulfuric acid testing (1.5% to a maximum of 2.5% lining mass loss).
Brick Shapes
We can shape ceramics in any way
In the design of refractory linings, flexibility and the ability to adapt the lining's shape to the specific shell and installation conditions play crucial roles. Thanks to our versatile molding department, large series reaching thousands of pieces and short runs, including a few pieces of complex ceramic shapes, pose no challenge for us.
We are involved in both the design and production of all necessary molds. For each shape, we prepare a detailed execution drawing. Over more than 170 years of activity, our specialists have developed documentation and a parts database, enabling the execution of over 35,000 shapes on demand without producing new elements.
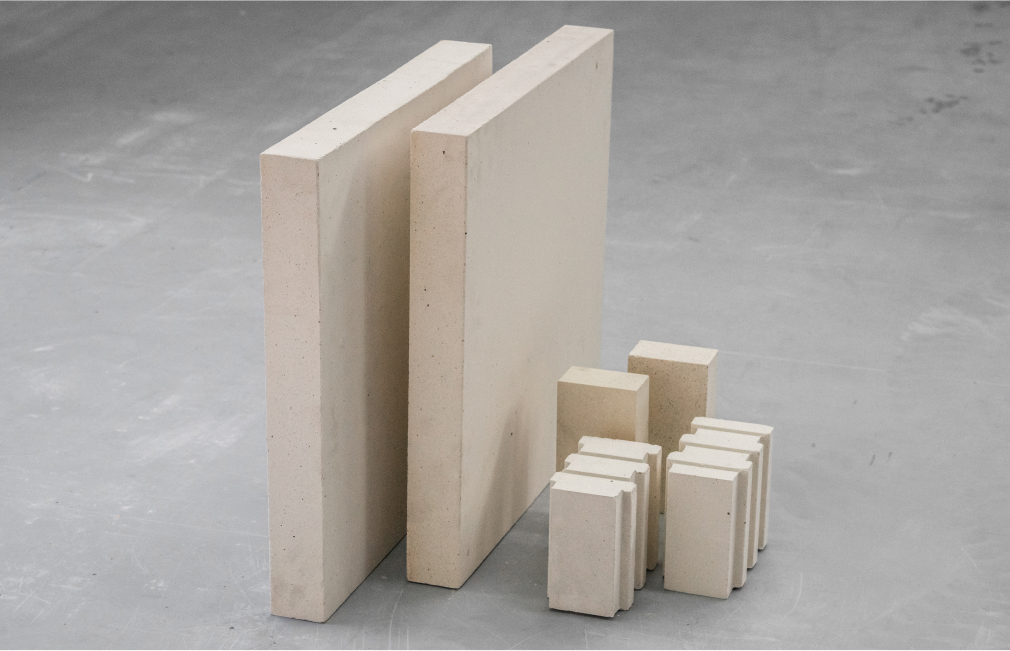
Why choose our refractory bricks
Predictable and consistent product quality
Thanks to our multi-point quality control plan, we ensure that every batch of refractory materials delivered meets the specified order conditions. This applies to both the product's shape and the series' size.
Broad portfolio of fire brick grades
We offer many types of bricks, from standard chamotte products to specialized high-alumina products. Our experts will help select the best product for the furnace lining's working conditions, reducing the risk of purchasing bricks unsuited to the furnace and the specified budget. We provide a warranty for the lining's operation over a specified period for selected applications.
Large mold stock and shape design service
We can produce all standard product formats, both simple and complex, without additional tooling costs for the client. Where a new product design is needed, we offer the experience of our designers, who will develop the best shape for the specific lining.
Own R&D department and laboratory
We have our own research and development (R&D) team and laboratory facilities. This allows us to provide our clients with technical support and advice, which is extremely important in solving complex technical problems. Our team of technologists and engineers offers the possibility of customizing products and services to meet individual client requirements.
High packaging standard
We undertake projects in over 40 countries across different continents. We ensure that our products arrive at the construction site in the same condition as they left the production line. Stable packaging allows for the safe stacking of pallets at the client's location on several levels.
Reliable raw material sources
We use primary and secondary sources in our raw material sourcing strategy. Primary raw materials are obtained from certified and verified suppliers and manufacturers worldwide. We generate secondary raw materials through the recycling of products and semi-finished products. Each raw material is subject to quality control, both on the supplier's side and at our premises upon delivery.
Production process and quality control steps
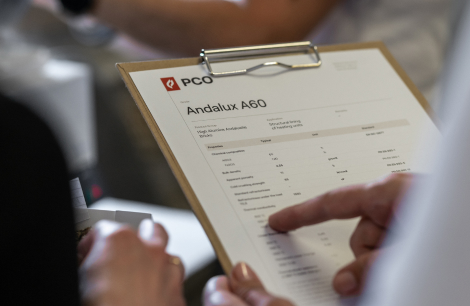
We control the quality of every delivered batch
Quality tests of each production batch are conducted in our fully equipped laboratory. These include checks of chemical composition, density, porosity, temperature resistance, expansibility, and thermal conductivity, which ensures the consistently high quality of our products.
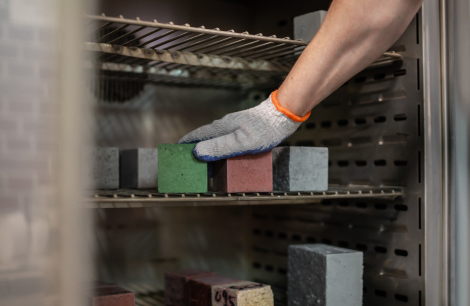
Transparent technical specification of products
Our Technical Data Sheets include a column with the product’s guaranteed properties. A dedicated Standard Tolerances document applies for each family of formed refractory products, clearly defining the quality framework without surprises.
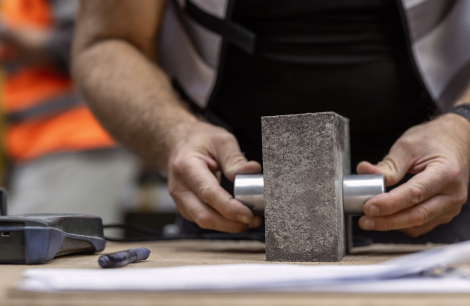
We issue international inspection certificates
We test and report product values according to commonly used industry standards, such as ISO and ASTM. Each order is documented with a type 3.1 certificate by the EN 10204 standard, available in selected languages.
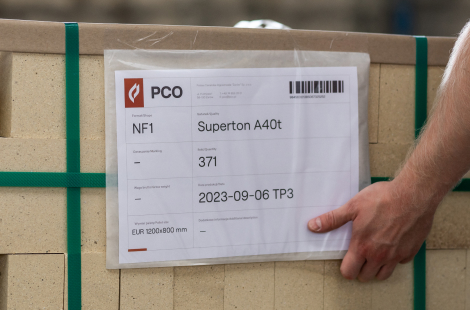
Insight into the production history of each product
All processes in our factory comply with the ISO 9001 management standard. An integrated ERP and workflow management system records every stage of production. Using barcodes, we have complete insight into each product’s history, enabling precise tracking of when and from which batch of raw material was produced.
Supplementary products
In addition to refractory ceramics for the working layer of linings, we also provide a range of additional products.
Do you need help deciding which material to choose or how to arrange the brick layers? Our engineers will perform a temperature flow calculation for you and suggest a layout from the working layer to the insulation layer.
Refractory mortars heatseting and airsetting, ready to use
Ceramic papers, thicknesses 1 to 5 mm
Bulk ceramic fiber, ropes and sealing joints
Semi dense insulating boards, thicknesses 10 to 100 mm
Calcium-Silicate boards
Ceramic fiber blankets, thicknesses 13 to 100 mm
Our offer
Contact us
Please select the option that best describes the subject you want to discuss with us. This will help us direct your inquiry to the right person at PCO.