Coke
Our offer for cokemaking industry
The coke industry faces challenges such as reducing CO2, SOx, and NOx emissions, fluctuating raw material prices, and adapting to changes in global steel demand.
These challenges necessitate increasing the efficiency of installations and constructing new, costly facilities to reduce environmental impact. PCO Żarów supports the industry by offering proven refractory lining solutions and producing aluminosilicate refractory products. Our bricks and shapes are manufactured according to customer specifications or standards such as DIN 1089-2. We handle both small-scale repair deliveries and large orders involving thousands of tons.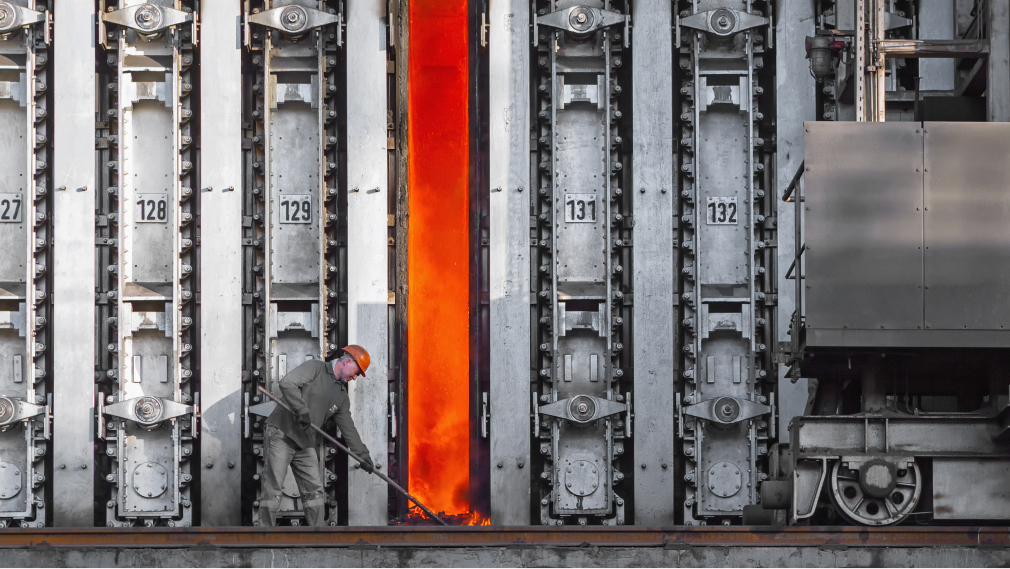
What we can do for you
Refractory lining design
- Thermal calculations using Simu-Therm for selected components of battery mass.
- Complete design and engineering package for refractory linings of reactors, including: detailed design (general layouts and details, reinforcement drawings, steel workshop drawings, component drawings, material sheets, bill of materials), installation instructions, drying curves and startup instructions, maintenance instructions.
- Inspection of refractory linings in reactors, regenerative areas, chamber doors, and furnace roofs.
- As-built documentation for repairs.
Production and supply
- Chamotte, quartz-chamotte, high-alumina, and insulating materials for regenerative heat exchangers, combustion chambers, chamber doors, and coke battery roofs.
- Ceramic linings for reactors used in catalytic NH3 decomposition and sulfur recovery units (SRU).
- Ceramic linings for coke unloading wharfs and settlers.
- Chamotte, high-alumina, and insulating linings for coke dry quenching (CDQ) installations.
- Ceramic linings for battery roofs, regenerators, flue gas channels, and chimneys.
- Refractory concretes and masses, including those for coke battery door linings.
Installation services
- On-site installation of new firing furnaces, CDQ installations, reactors, ceramic linings for coke wharfs, ceramic gas channels, and chimney linings.
- Repairs and reconstructions (demolition and removal of ceramic scrap, ongoing repairs of chambers, heaters, batteries, and reactor linings).
- Supply of all necessary supplementary materials.
- Project planning and management.
Furnaces and high-temperature industrial equipment
Coke oven battery
A coke battery is a complex furnace system where coal is subjected to pyrolysis at temperatures exceeding 1200 °C. Refractory materials serve both structural and technological functions here, being exposed to extreme thermal, erosive, and corrosive conditions. Our offering includes a complete material solution for the coke battery structure.
Scope of offer: Lining design Refractory products supply Lining installation services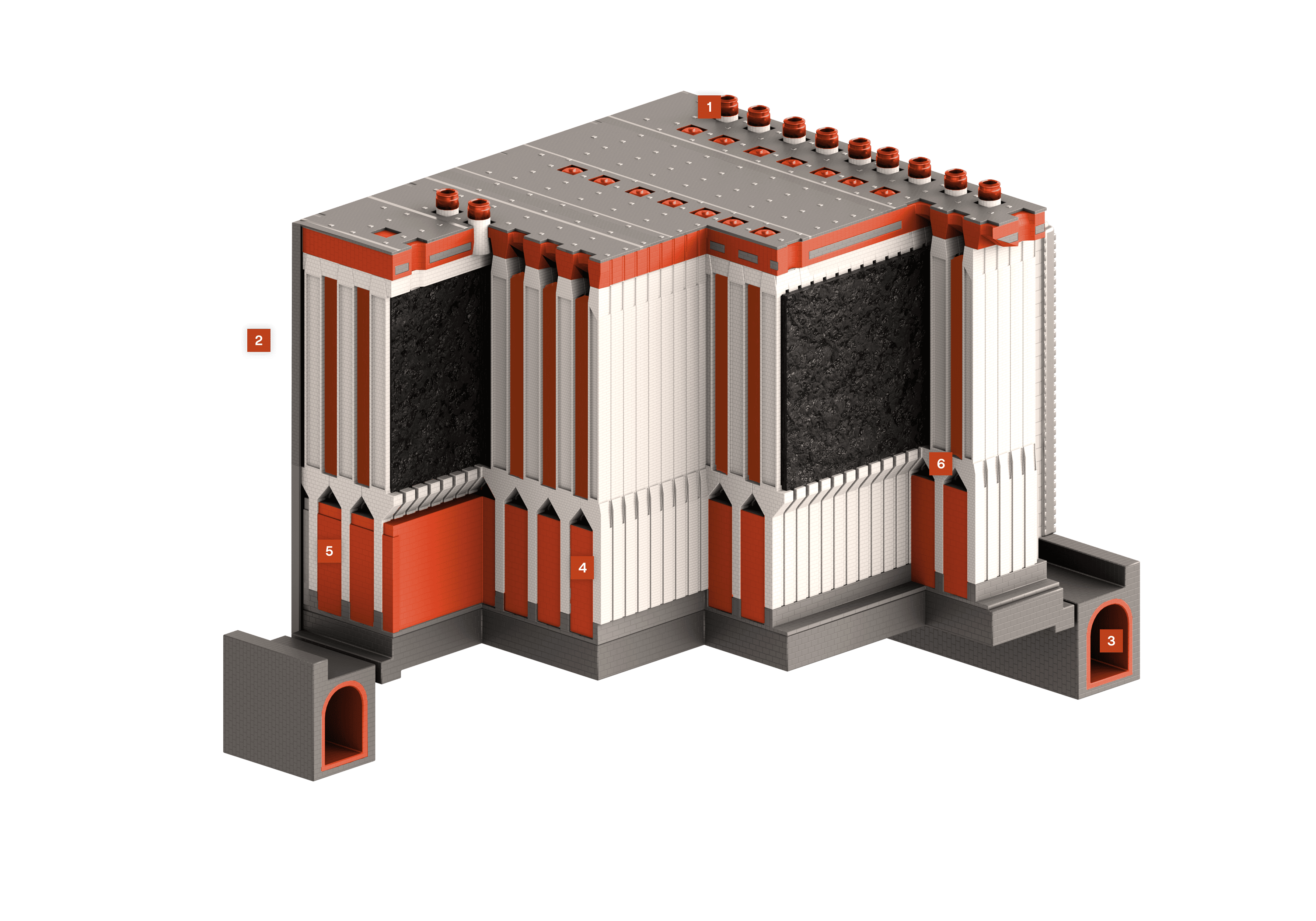
The materials used for the roof must have excellent insulating properties and the appropriate density. We have developed ISOLUX insulating materials and higher-density products that stabilize the battery chambers. The final roof layer, resistant to variable conditions and wear, is made of RESIMAX material, which offers high mechanical strength and low water absorption.
Exposed to cyclic temperature changes, the doors must be made from materials resistant to thermal shocks. We have developed KORMAX and PCOCAST materials, based on amorphous silica and cordierite, which enhance the durability of the doors. These materials are produced in the form of shapes, concrete prefabricates, or castable materials for on-site casting.
Both flue gas channels and coke battery chimneys are exposed chemical corrosion caused by the presence of acidic oxides and dust in the flue gases. For those areas we recommend RESIMAX materials with reduced water absorption and increased resistance to acid corrosion.
In the area beneath the coke oven chambers, we use SITONEX quartz-chamotte material, which provides minimal secondary shrinkage, improving the sealing of the regenerator lining. Checker bricks are produced with precisely defined geometry and tolerances, facilitating their installation.
To minimize heat loss through the chamber end closure areas, we use lightweight ISOLUX insulating products with a locking system that improves sealing and reduces heat transfer to the outside.
In the battery hearth area, where sudden temperature changes are most likely, we offer special products with enhanced resistance to thermal shocks (TSR bricks). Our developed material features a high mullite phase content, providing high resistance to temperature fluctuations.
What can we help with?
If you would like to receive free advice or inquire about the selection of refractory linings, leave us your contact details, and we will call you!
Send an inquiryDeformations and dimensional deviations of shapes prevent quick and airtight assembly of the structure.
Limited availability of refractory materials due to the large format and complexity of shape models.
The need to use materials with low secondary shrinkage to maintain the tightness of the lining.
Coke wharf
The coke wharf and settler are integral components of a traditional coke plant using the wet quenching method. Their functions include draining excess water from the coking coal, cooling the hot coke before further transport, and helping to control the amount of coke falling onto the conveyor belt.
Scope of offer: Lining design Refractory products supply Lining installation services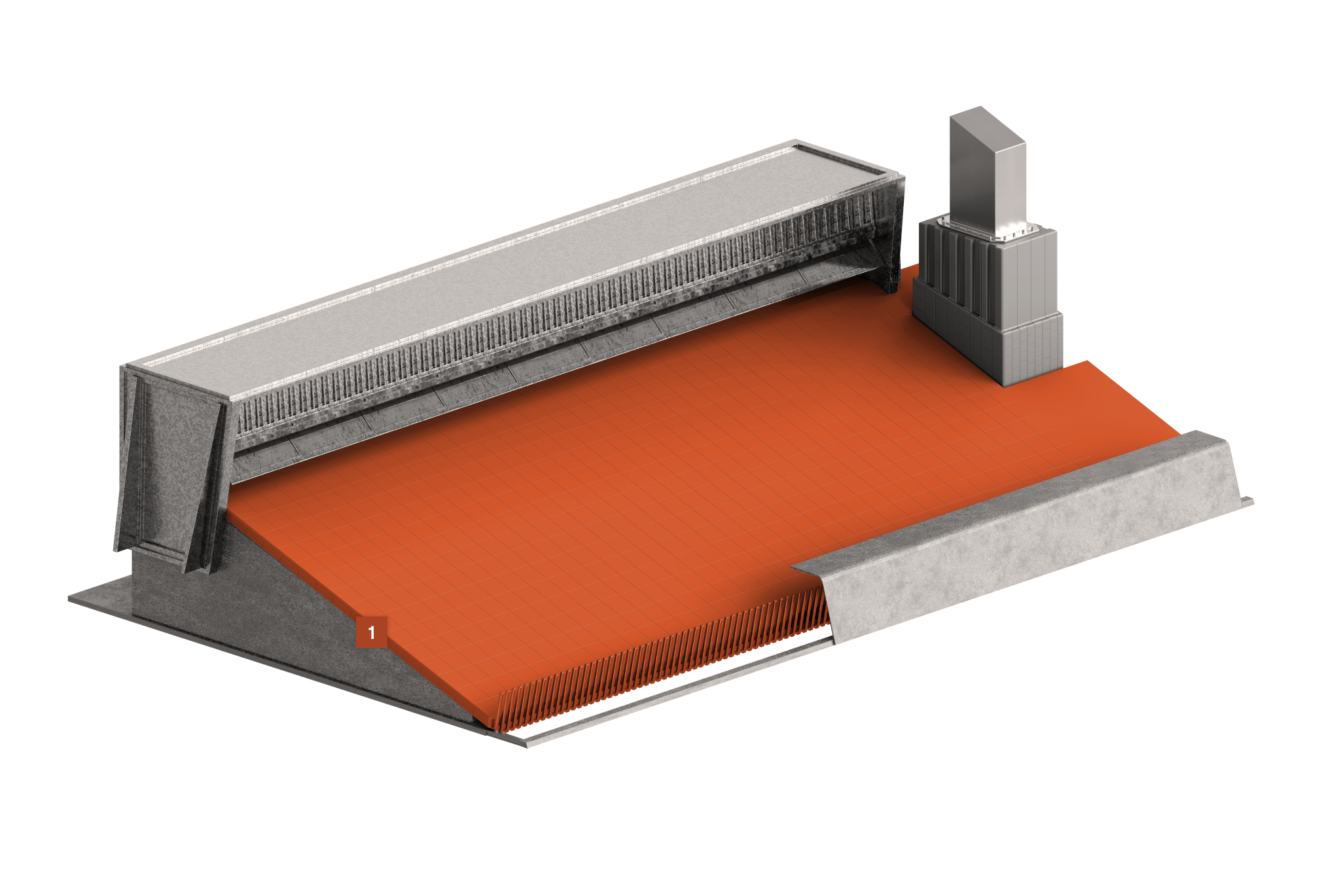
The lining of the coke chute is primarily exposed to elevated temperatures, sudden temperature changes (thermal shocks), strong mechanical impacts, and the erosive effects of falling coke. For these conditions, we have developed the ABRAL ŻRMK corundum-zirconium material.
What can we help with?
If you would like to receive free advice or inquire about the selection of refractory linings, leave us your contact details, and we will call you!
Send an inquiryCoke getting stuck during discharge, caused by wear and tear in the lining.
Coke getting stuck during discharge due to the rough surface of the chute ramp.
Year-round operation in environmental conditions (frost resistance of the refractory lining).
Coke Dry Quenching
Coke pushed from the coke oven chambers must be cooled to enable safe transport and further processing. This stage of the process can be carried out through a coke dry quenching installation. In this installation, the coke is cooled by contact with a circulating inert gas, usually nitrogen, instead of traditional wet quenching with water. This method not only protects the environment by reducing dust emissions but also provides energy benefits through the recovery of heat from the hot coke. The refractory materials used in the lining of this installation must exhibit good resistance to mechanical impacts (abrasion, impact) and thermal shocks.
Scope of offer: Lining design Refractory products supply Lining installation services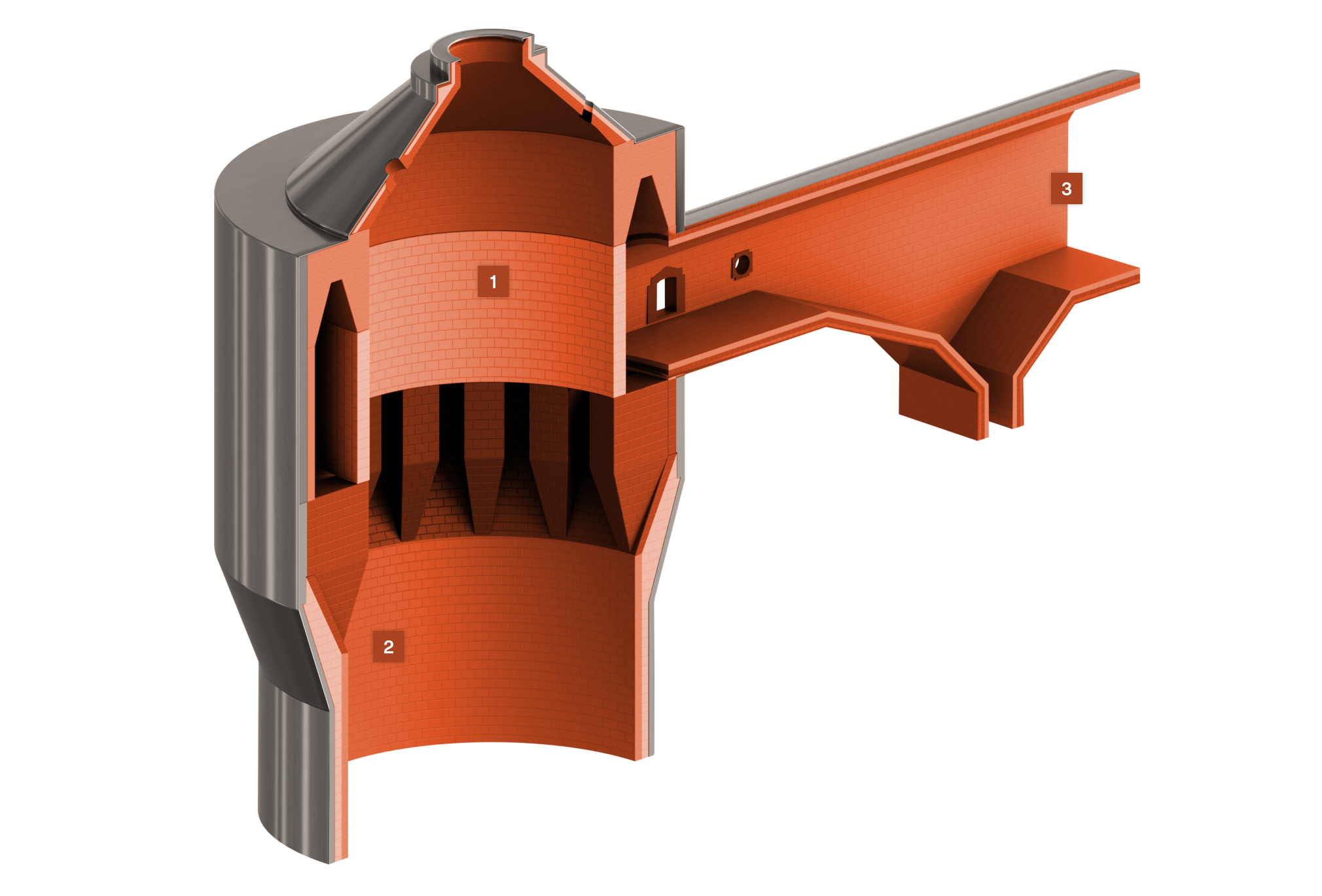
This area of the installation experiences some of the most challenging conditions in the entire system. These include extremely high temperatures (approximately 900–1000°C) due to the introduction of fresh, hot coke, severe thermal shocks from the cyclic loading of hot material, and intense mechanical stresses caused by the impact of coke during loading. Due to these demanding conditions, we recommend using products from the ANDALUX or SUPERTON series, which are characterized by a high mullite phase content, providing excellent mechanical and thermal resistance. For the insulating layers, we suggest a combination of light and heavy insulation from the ISOLUX series, which effectively minimizes heat loss while withstanding the harsh working conditions.
While the conditions in this part of the installation are somewhat less extreme than in the quenching chamber, they still present several challenges for the refractory lining. Temperatures in this chamber range from 600–800°C, gradually decreasing as the coke cools. The constant flow of inert gases can lead to erosion of refractory materials, and the moving coke imposes abrasive mechanical loads. Shapes and wedges from the ANDALUX and SUPERTON families are well-suited for this section, providing optimal resistance to abrasion and erosion. For the insulating layers, materials from the ISOLUX family are recommended, offering effective thermal insulation and long-lasting durability under demanding conditions.
The role of this part of the installation is to remove and control the amount of dust generated during the coke cooling process. These dust particles can pose environmental hazards and negatively affect the efficiency and longevity of the entire installation. The refractory linings in this section are subjected to stresses such as gas flows containing large amounts of dust and coke particles, uneven temperature distribution with the potential for localized hot spots, and corrosion of materials due to contact with chemical components in the gases and dust. PCO recommends materials from the ANDALUX, SUPERTON, and NORMATON families, which ensure long-lasting and reliable operation due to their high abrasion resistance, low porosity, and excellent resistance to thermal shocks. Additionally, these materials exhibit strong chemical stability, minimizing the risk of material degradation in an aggressive working environment.
What can we help with?
If you would like to receive free advice or inquire about the selection of refractory linings, leave us your contact details, and we will call you!
Send an inquiryContinuous flow of hot gases and dust leads to erosion of the refractory lining surface.
Cyclic temperature changes cause the formation of microcracks and material degradation.
Coke combustion products may contain chemicals that react with refractory materials, accelerating their wear.
Reactor for the catalytic decomposition of ammonia and sulfur production using the Claus process
A reactor for the catalytic decomposition of ammonia and sulfur production using the Claus process is a critical component in the sulfur recovery process from waste gases and plays a vital role in reducing harmful emissions to the atmosphere. Due to the complex operational conditions, the refractory lining in this reactor faces several significant challenges.
Scope of offer: Lining design Refractory products supply Lining installation services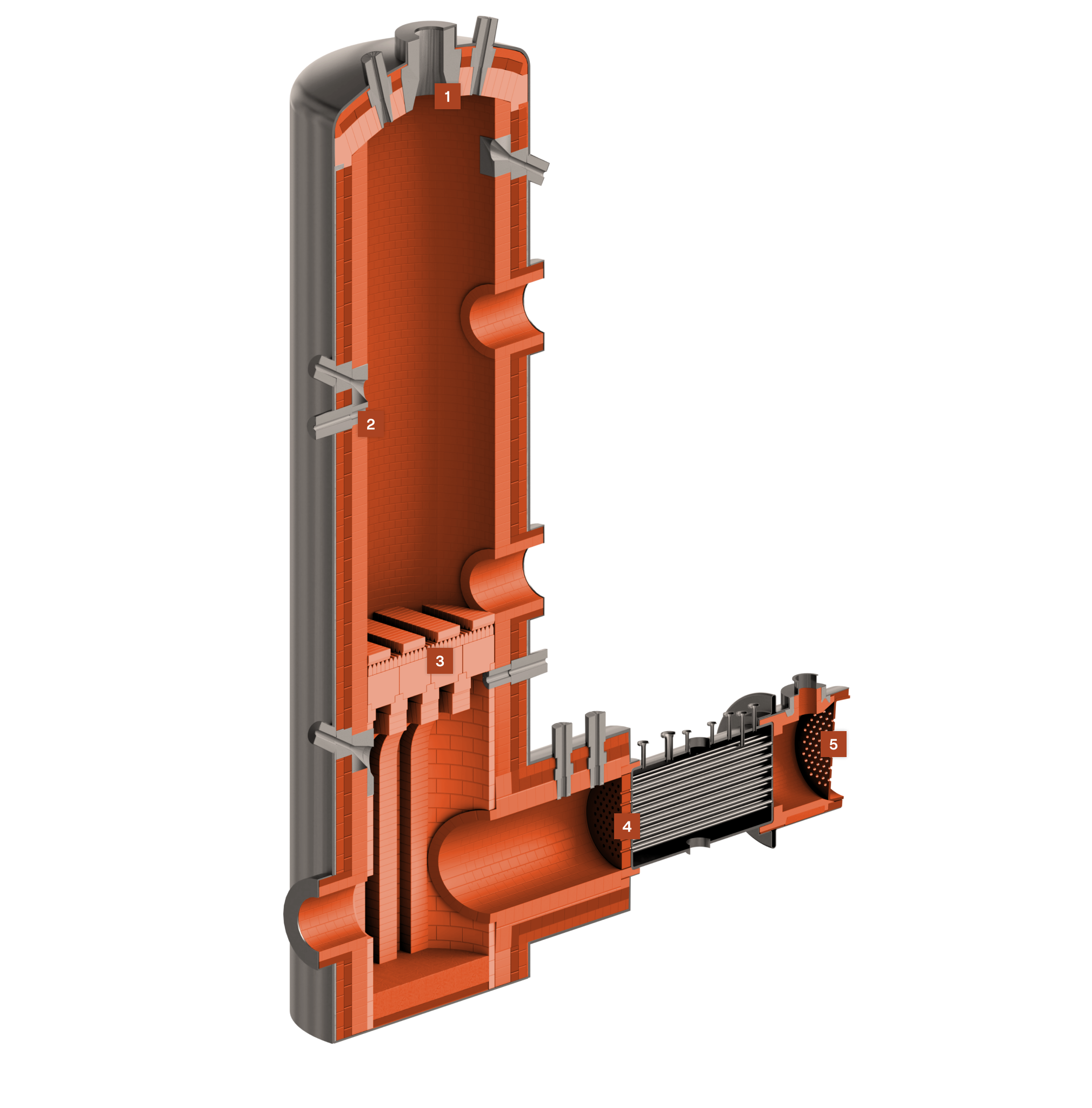
The intense heat generated during operation and startup creates thermal stresses in the burner's ceramic parts. The burner material must be resistant to thermal shocks and localized extremely high temperatures.
This section of the reactor is also exposed to high temperatures, although typically lower than in the burner. The primary challenge here is the prolonged exposure to reactive gases. The presence of SO2 and other sulfur compounds can lead to chemical corrosion, weakening the refractory material over time, which may result in the penetration of the insulating layers and thermal disturbances in the reactor’s operation or damage to the steel casing.
The ceramic bed operates at high temperatures and supports the catalyst bed. It is exposed to the direct impact of hot gases and the weight of the catalyst material. The refractory lining must have high stability at elevated temperatures and good chemical resistance to process gases.
The sieve floor must ensure adequate sealing and insulation of the refractory lining while enabling proper installation and operation of corundum tubes from the high-pressure boiler.
In this part, the refractory lining is primarily exposed to high temperatures and potential chemical corrosion from reactive compounds remaining in the gas.
What can we help with?
If you would like to receive free advice or inquire about the selection of refractory linings, leave us your contact details, and we will call you!
Send an inquiryUnder certain operating conditions, sulfuric acid condensation may occur, leading to chemical corrosion of the refractory lining.
Improper or insufficient insulation of the steel reactor casing can cause overheating of the shell.
Difficulty finding a specialized/experienced installation company.
Why choose PCO?
We Produce Any Shape
Dimensional Consistency Regardless of Production Series Size
Experienced Bricklaying Team
Selected Products and Services for the Coke Industry
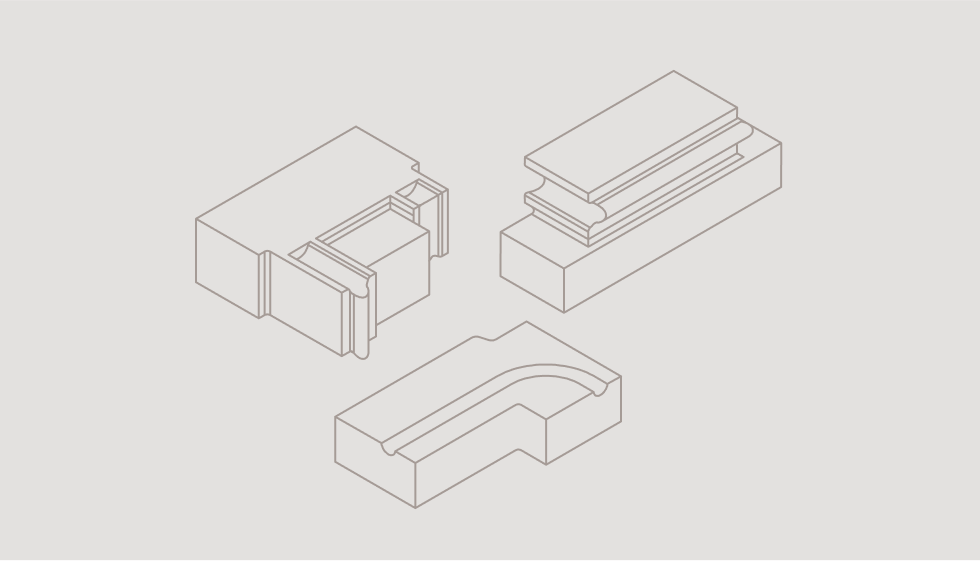
SITONEX
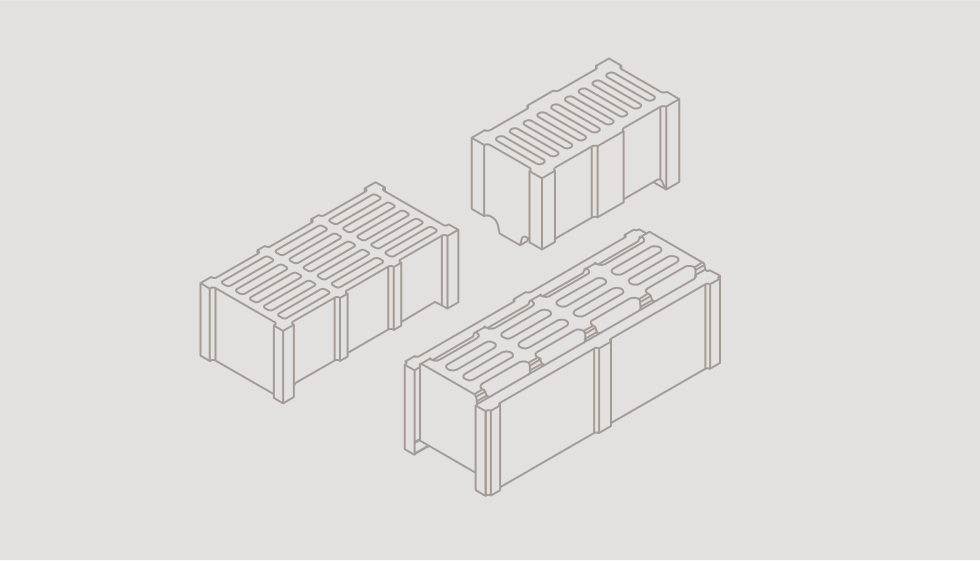
Checker Bricks
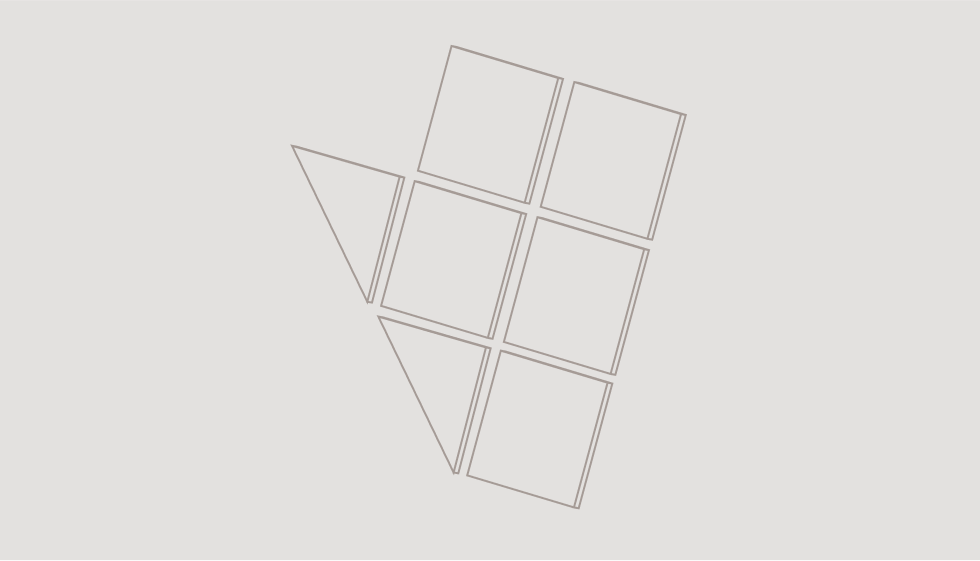
ABRAL ŻRMK
Contact us
Please select the option that best describes the subject you want to discuss with us. This will help us direct your inquiry to the right person at PCO.