Refractory castables, masses, and mortars
Our portfolio of refractory materials
We produce dense and insulating refractory concretes, mortars, and masses for applications ranging from 600 °C to 1700 °C.
All our products are based on high-quality raw materials, such as chamotte, bauxite, mullite, andalusite, and corundum. Refractory monolithic products are unique blends that maintain their properties while resisting high temperatures. They are used where the application of formed products (refractory bricks) is impossible.
We offer complete monolithic solutions, including dense and insulating concrete, tailored to various installation methods, such as casting, shotcreting, and ramming. We propose materials based on cement, silica, gel, or hybrid bonding systems depending on the customer's needs.
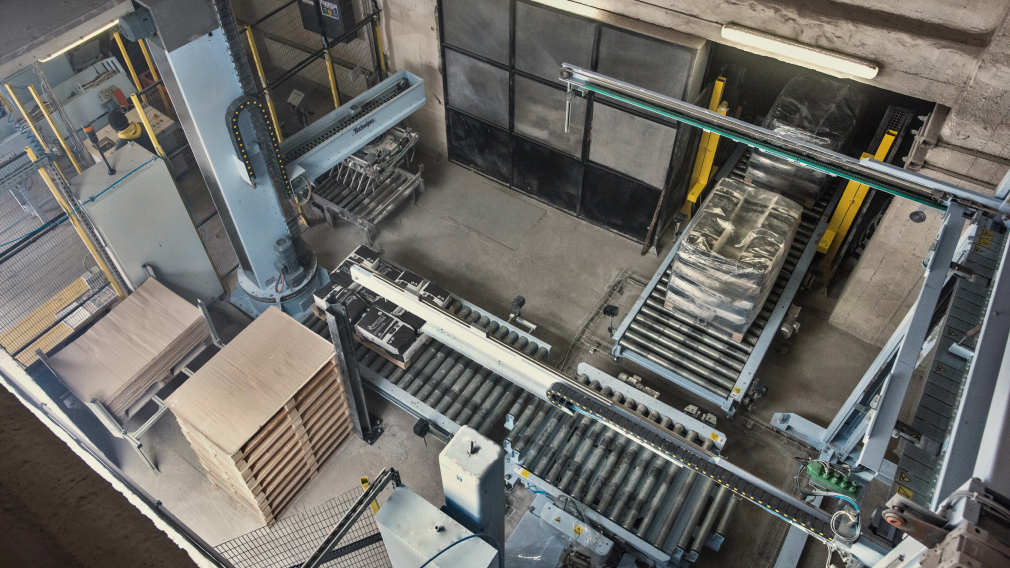
Our products
Castable refractory
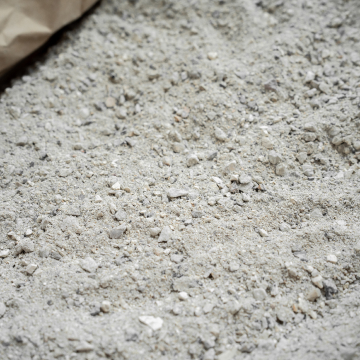
Casting concrete is a refractory material that is supplied in powder form. After mixing with a liquefier, most often water, it is poured into molds or casting forms to achieve a specific shape of refractory lining. Available mixes include traditional, vibrated, and self-leveling types, which do not require vibration. After drying and setting, such concretes acquire a solid structure, gaining resistance to mechanical factors and high temperatures. We supply these products in 25 kg paper bags or big bags with a 500 or 1000 kg capacity.
Conventional refractory concrete, with a high cement content (15-30%), is the easiest to install (correct mixing and drying) among casting concrete. Although they do not provide the highest performance in extreme conditions, they are a versatile and cost-effective choice for many standard operating conditions in refractory linings.
Medium refractory mortars castable concretes (MCC) achieve binding with a cement content ranging from 5 to 15%. They bridge the gap between conventional and low refractory castable concretes in terms of performance and workability. Specialists appreciate the suitable parameters achieved at low temperatures (even before startup) and the more workable consistency than low-cement alternatives or cement-free systems.
Low cement castable concretes (LCC) require a minimal morstars content (from 3 to 10%) to achieve binding. As a result, they need more attention during installation than, for example, conventional concretes, but a well-made lining is characterized by improved parameters such as higher temperature resistance, lower porosity, resistance to corrosion and abrasion, and thermal shock resistance.
The BN SiC line includes low cement castable concretes for special applications in areas most susceptible to thermal shocks and corrosive factors.
Cement-free refractory concretes (NCC) do not contain cement, and binding is achieved through additives such as silicates, aluminates, or phosphates. They are intended for applications at very high temperatures, where traditional cementitious concretes could degrade. Linings made from cement-free concretes are characterized by, among other things, high resistance to thermal shocks and chemical corrosion.
Gunning mixes
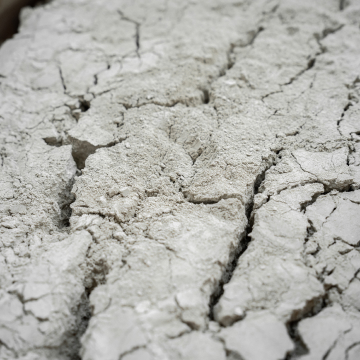
Gunning mix is a product used in the method of pneumatically conveying the refractory mix through a hose. To this mix is added a liquefier, most often water. Then, the mix is sprayed onto the application surface at high velocity. Our portfolio includes materials based on binding systems that utilize both cement and special chemical additives.
The PCOGUN line of masses is designed to be easy to apply and adhere well to the existing lining. The products are characterized by specially selected granulation and contain additives that minimize material loss during spraying (reduced rebound).
Insulating casting concrete
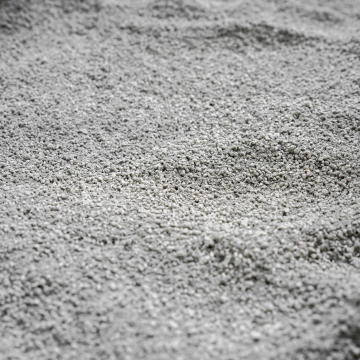
Light insulating concrete is a specially designed monolithic product that combines excellent insulating properties with the integrity of the refractory lining.
Thanks to its porous structure, it has a low density, which translates into lower thermal conductivity, making it harder for heat resistance to penetrate. As a result, it offers better insulation than dense concrete.
Insulating concretes in the ISOCAST line are available in versions with densities ranging from 0.6 to 1.4 g/cm³ and are designed to operate in temperature ranges from 600 °C to 1450 °C. They are produced based on lightweight clays and shales. Although not as durable as dense concretes, they still provide sufficient mechanical strength for many applications in insulating layers of refractory linings.
Insulating gunning mixes
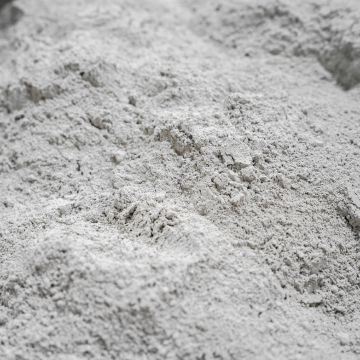
Insulating gunning mix is a product used in the spray method. In this method, the refractory mix is pneumatically transported through a hose, and a liquefier, usually water, is added. The mix is then applied to the application surface at high velocity.
Similar to the casting versions, ISOGUN insulating spray masses are available in densities ranging from 0.6 to 1.4 g/cm³ and are designed to operate in temperatures from 600 °C to 1450 °C. The masses are easy to apply and contain additives that minimize material loss during spraying (reduced rebound).
Refractory ramming mass
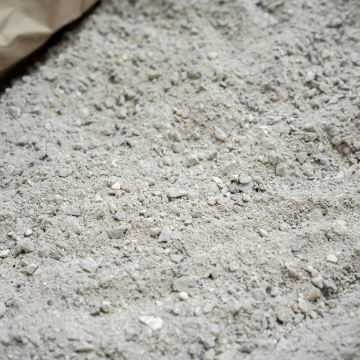
Refractory ramming masses are unique blends of materials with plastic properties. They are supplied in moist form, either loose in bags or as blocks.
After application to the appropriate surface and drying, the mass hardens. After undergoing proper thermal treatment, it becomes resistant to high temperatures and mechanical factors.
Moist refractory masses based on chamotte raw materials are intended for minor current repairs of chamotte masonry. They are supplied loose in bags or as lumps for ramming with a hammer.
Moist refractory masses based on high-alumina raw materials are intended for minor current repairs of high-alumina masonry. They are supplied loose in bags or as lumps for ramming with a hammer.
Refractory mortar
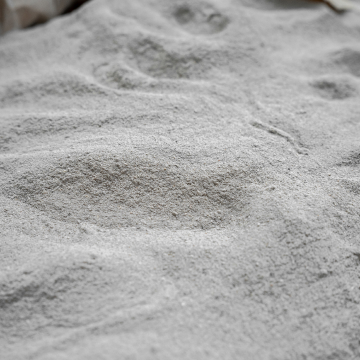
Refractory mortars are high-quality aggregate and refractory clay mixtures designed for joining refractory bricks in linings. Their application is essential for the durability and safety of ceramic linings. It is crucial to use the appropriate refractory mortar compatible with the refractory materials used, as it ensures the masonry exhibits minimal binding expansion.
Like traditional masonry mortars, refractory mortars are applied in a wet state and, after use and drying, create durable and tight joints. Various types are available, including mortars with a ceramic bond, e.g., requiring heat treatment at a minimum temperature of 600 °C, known as heat setting, and those with a chemical bond, which hardens upon contact with air, known as air setting.
The dry refractory mortar line MORTALEX is designed to supply an appropriate mortar for every type of brick produced by PCO. Such a combination ensures uniform properties in every layer of the lining. Ceramic bond (headset) mortars require mixing with water, and the bond gains strength only after the lining is heated to a specified temperature.
PCO offers air-setting mortars for every working temperature range. These mortars are supplied in dry form and applied by adding water and application. Unlike ceramic bond mortars, to achieve a durable joint, it is not necessary to heat the lining, as bonding occurs at room temperature.
MORTALEX refractory wet mastics are ready-to-use adhesives for joining fire bricks and lightweight insulation products (calcium silicate and semi-dense boards). Their advantage is that the joint gains strength immediately after application without the need to perform heating-up.
Dry insulating mortars MORTISOL are the right choice for joining fire bricks. Using a dedicated mortar ensures uniform properties throughout the insulating layer – the temperature flow profile between the brick and the mortar is similar.
Why choose our refractories
Stable product quality
We ensure the stable quality of our products through a multi-point quality control plan that guarantees each batch complies with established tolerance limits, regardless of the product shape and series size.
Dryout curve recommendation
Recommendations for the heating curve are crucial for achieving optimal properties of monolithic products after thermal processing. Our experts can adjust the temperature increase curve to the specific type of monolithic lining, ensuring ideal startup conditions.
Expert supervision during concrete installation
We provide instructions for preparing and applying each of our refractory concretes along with delivery. Proper preparation of the mix, application, and drying of the monolithic lining is crucial for the device's correct operation. A PCO specialist can be present on-site during the refurbishment and advise on adequately preparing and installing the refractory mass lining.
Own R&D department and laboratory
Our R&D department and specialized laboratory allow us to offer dedicated technical support and advice. This is particularly important in solving challenging technical problems. Our team of technologists and engineers enables the customization and adaptation of products and services to meet clients' unique needs.
Wide range of products and application methods
We have a wide range of products and applications, producing concretes based on various binding systems, such as cementitious, gel, silica, or hybrid. We supply products adapted to the conditions of a given refurbishment, enabling multiple application methods, such as casting, shotcreting, or ramming. Our products are easy to install and start, ensuring efficiency in every refurbishment project.
Reliable raw material sources
We utilize primary and secondary sources in our raw material sourcing strategy. Primary raw materials are always obtained from certified, vetted suppliers and manufacturers worldwide. Secondary raw materials are generated through the recycling of products and semi-finished products. Each raw material undergoes rigorous quality control upon delivery, both on the supplier's side and with us.
Production process and quality control steps
Supplementary products
In addition to refractory ceramics for the working layer of linings, we also provide a range of additional products.
Do you need help deciding which material to choose or how to arrange the brick layers? Our engineers will perform a temperature flow calculation for you and suggest a layout from the working layer to the insulation layer.
Refractory mortars heatseting and airsetting, ready to use
Ceramic papers, thicknesses 1 to 5 mm
Bulk ceramic fiber, ropes and sealing joints
Semi dense insulating boards, thicknesses 10 to 100 mm
Calcium-Silicate boards
Ceramic fiber blankets, thicknesses 13 to 100 mm
Our offer
Contact us
Please select the option that best describes the subject you want to discuss with us. This will help us direct your inquiry to the right person at PCO.