Cement, lime and paper
Our offer for cement, lime and paper industry
The calcination of calcium carbonates and their subsequent thermal processing play a pivotal role across multiple industries, especially construction and chemical manufacturing.
Cement clinker and quicklime are essential components of building materials, and quicklime is also widely used in industrial processes such as pulp production, soda manufacturing, and sugar refining. Today, these processes face intense pressure to maximize efficiency and meet sustainability goals. CO₂ emissions from raw materials significantly impact the economics of calcination, making efficiency at every stage crucial. Uninterrupted production campaigns, minimized downtime for maintenance, and thermally efficient kiln linings can deliver a significant competitive advantage. PCO’s mission is to support our partners with refractory‐technology solutions for lime and cement kilns—from engineering studies and collaborative selection of optimal refractories and installation methods to global logistics, installation, and supervision. We believe that the dependable quality of our products and services, combined with comprehensive support, helps minimize production interruptions and empowers our partners to achieve greater competitiveness and their sustainability objectives.
What we can do for you
We design
- The selection of appropriate refractory grades tailored to your production‐process conditions
- The optimal configuration of the refractory lining, taking into account the equipment’s design, process zones, operating conditions, and user preferences
- Thermal‐flow analyses for different lining alternatives (A/B comparisons)
- Lining‐structure optimization to extend service life and reduce heat losses
We manufacture and supply
- Chamotte and high alumina refractories with enhanced abrasion resistance, designed for lining heat‐exchange towers, third‐air ducts, calciners, riser ducts in cement plants, and cooler inlet and outlet zones in lime kilns.
- Innovative low‐cement and cement‐free castables for a wide range of applications in cement plants, enhanced with additives such as SiC and ZrO₂.
- Insulating products for protective layers in shaft and rotary kilns, including grades with increased mechanical strength.
- Prefabricated refractory modules ready for installation without the need for on‐site heat‐up procedures.
We install
- Dismantling and installation of linings in all cement‐production plant equipment, as well as shaft and multi‐shaft kilns
- Removal and collection of dismantled refractory lining (refractory scrap)
- Routine repairs and emergency maintenance during overhaul campaigns
- Technical consulting—failure‐cause analysis, lining‐life optimization, and supervision of refractory installation
Furnaces and high-temperature industrial equipment
Upper cyclone stages
The upper cyclones play a crucial role in the clinker production process by properly mixing, transferring, and distributing raw‐material particles. In this zone, the material is gradually heated, with temperatures reaching up to 600 °C. The process runs continuously, demanding durable, wear‐resistant refractories. Structurally, a cyclone lining can be divided into three main areas: the dome, the barrel, and the cone. The greatest challenge for the refractory lining here is abrasion from the intense flow of raw materials, while the impact of high temperature is relatively minor. Because upper cyclones undergo very long repair cycles—lasting from decades to many decades—it is essential to use exceptionally durable materials. Under standard conditions, chamotte bricks such as NORMATON are used; in areas subject to heavy abrasion, high-abrasion chamotte like EXTRATON is recommended. In some installations, refractory castables are also employed to provide additional wear resistance and dimensional stability.
Scope of offer: Lining design Refractory products supply Lining installation services
The refractory lining of the upper cyclone dome is primarily exposed to gas‐borne abrasion caused by entrained particles in the feed. In this zone, the effects of temperature and mechanical stresses are minimal, resulting in relatively mild service conditions. The dome lining is constructed in multiple layers, with wedge‐shaped bricks forming both the working and insulating layers. This multilayer design provides effective gas protection while minimizing wear of the lining material. Given the low‐demand operating environment, low‐alumina EXTRATON products and lightweight ISOLUX insulating bricks perform exceptionally well in this zone, offering sufficient resistance to gas abrasion while maintaining optimal thermal‐insulation properties.
The lining of the barrel (cylindrical section) of the upper cyclone is subjected to both abrasive and mechanical wear, although these conditions are relatively mild. Mechanical stresses are moderate, allowing for the use of standard refractory solutions. The barrel lining is constructed much like the dome—comprising multiple layers, with wedge bricks dominating both the working and insulating layers. This design permits an even distribution of loads and ensures long‐lasting protection against abrasion. Under these moderate service conditions, the same products used for the dome—the low-alumina EXTRATON series and lightweight ISOLUX insulating modules—are suitable here as well, providing adequate resistance to abrasion and mechanical action while maintaining effective insulation.
The cone is the most mechanically stressed part of the cyclone, although overall the risk to the refractory lining remains low. This is due to the zone’s shape, which influences the intensity of mechanical forces. Because of the cone’s complex geometry, the lining is constructed from castable refractory concrete, allowing the material to conform to the difficult shape and simplifying installation. This design must ensure even distribution of the refractory on the irregular surfaces.
What can we help with?
If you would like to receive free advice or inquire about the selection of refractory linings, leave us your contact details, and we will call you!
Send an inquiryHow to minimize spalling of alumina bricks under rapid thermal cycling from preheated raw meal?
Which monolithic stamping material best resists abrasion by high‐velocity particulate?
How to prevent alkali‐induced corrosion and salt attack on the lining surface?
Lower cyclone stages
The lower cyclones play a crucial role in the clinker production process by providing intensive mixing, transfer, and distribution of raw‐material components. In this zone, temperatures can reach up to 950 °C, meaning the material is subjected to higher temperatures than in the upper cyclones. A key aspect of lower cyclones is the partial precalcination of limestone, which enhances the efficiency of subsequent process stages. Structurally, the refractory lining of the lower cyclones consists of a dome, a barrel, and a lower cone. In this part of the installation, refractories face far more aggressive conditions than in the upper cyclones. Under standard conditions, multi-chamotte bricks with andalusite and silicon-carbide additives from the EXTRATON and ABRAL lines are employed, offering high abrasion and alkali resistance. When castable linings are used, GELCAST, MULCAST, and NxGel products are recommended for their superior resistance to alternative fuels and aggressive chemical environments.
Scope of offer: Lining design Refractory products supply Lining installation services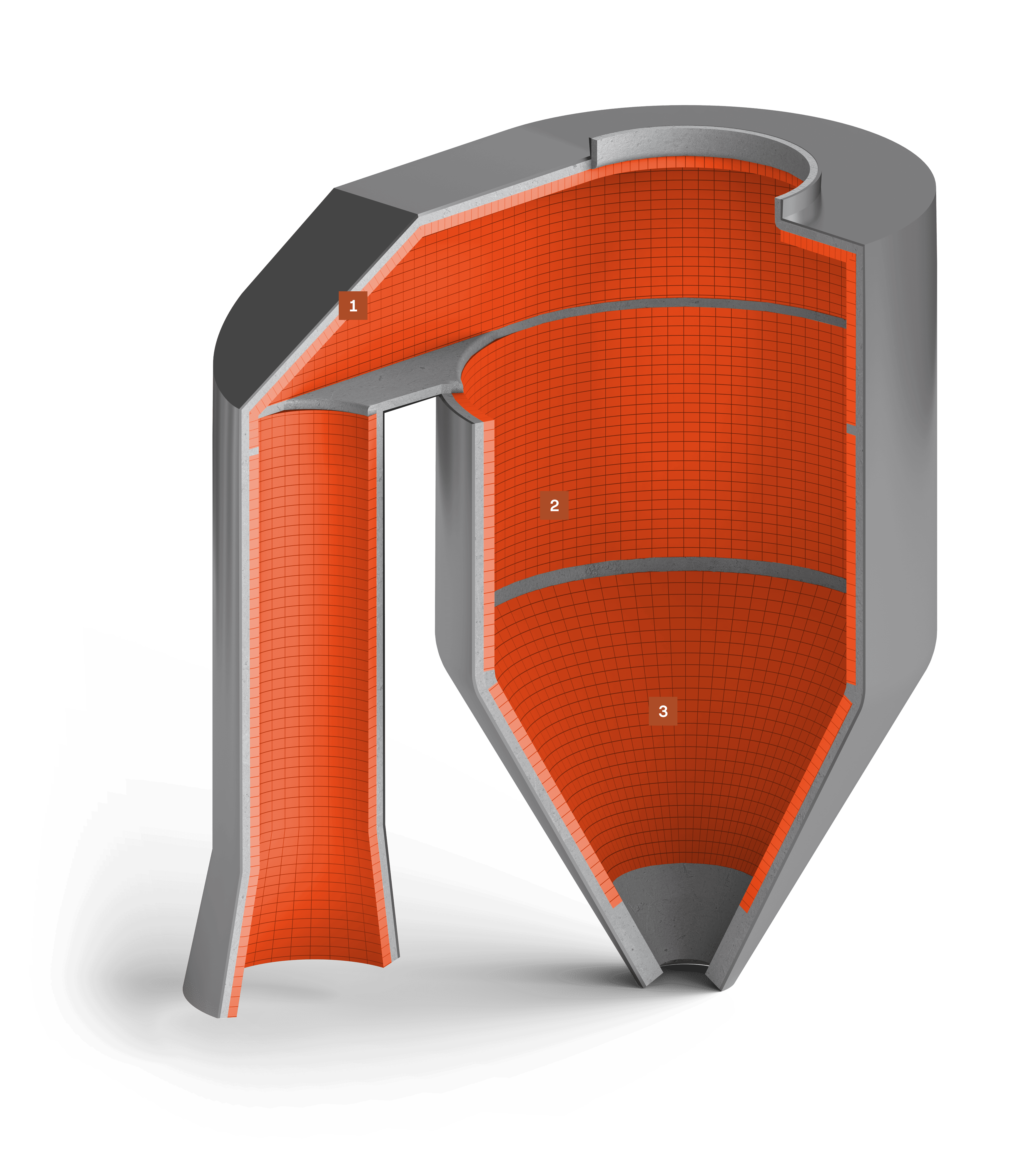
The lining of the lower cyclone dome is primarily exposed to gas-borne abrasion from volatile feed particles. Although the effects of temperature and mechanical forces are relatively minor, service conditions are more demanding than in standard upper cyclones. In addition, the lining must resist chemical attack and accretion from deposits, which increases the risk of degradation. The dome lining is built in layers—several overlapping strata in which wedge bricks play a key role in both the working and insulating layers. This structure allows for gradual load distribution and provides superior protection against both chemical attack and abrasion.
The lining of the barrel (cylindrical section) in the lower cyclone is subjected to a combination of stresses—abrasion, mechanical wear, and aggressive chemical attack, including alkali corrosion. Such multidirectional loading demands a lining that resists both severe mechanical erosion and chemical degradation, making the operating conditions in this zone particularly challenging. Like the dome, the barrel lining is built in multiple layers, with wedge bricks dominating both the working and insulating strata. This multilayer construction ensures even distribution of mechanical and chemical stresses, thereby extending the service life of the lining.
The cone, as the part of the lower cyclone, is the most heavily stressed zone in terms of mechanical, chemical, and abrasive forces. Due to the challenges posed by the cone’s unusual geometry and the complexities of brick installation, the lining in this zone is executed with cast refractory concrete. This approach allows the material to be fitted precisely to the cone’s intricate shape, minimizing the risk of uneven stresses and localized damage. In the cone area, it is essential that the refractory offers resistance to mechanical, chemical, and abrasive loads.
What can we help with?
If you would like to receive free advice or inquire about the selection of refractory linings, leave us your contact details, and we will call you!
Send an inquiryWhich castable offers the optimal balance of abrasion resistance and thermal shock tolerance?
How do we control differential expansion between ceramic brick and steel shell to avoid joint cracking?
How to prevent dust buildup on the refractory lining?
Calciner
The calciner, used primarily for the preheating and calcination of limestone raw materials, shifts part of the combustion and decarbonation process from the rotary kiln into a tower of heat exchangers. By utilizing alternative fuels, the calciner reduces gas emissions and lowers operating costs. However, its operating conditions are significantly harsher, demanding advanced refractory materials. Temperatures in the calciner range from 800 °C to 1100 °C, and the calciner duct is exposed to high heat as well as corrosive agents—SOₓ, NOₓ, alkalis, chlorine, and sulfur—that lead to abrasive wear of the lining. For this reason, low-cement or cement-free castables enriched with zirconia and silicon carbide are employed, and spray-applied castables may be used for repairs. In brick linings, high-alumina products resistant to chemical attack, elevated temperatures, and thermal shock are recommended. The calciner lining is multi-layered—comprising a working layer, a protective layer, and an insulating layer—to ensure durability under extreme conditions. The maintenance cycle typically spans several years, depending on operating parameters and the share of alternative fuels.
Scope of offer: Lining design Refractory products supply Lining installation services
In this zone, temperatures range from approximately 700 – 900 °C. The primary risks to the refractory lining are mechanical abrasion and chemical erosion caused by the ingress of fine particles. Occasionally, accretions—mainly from sulfur and chlorine when using alternative fuels—form on the lining. High-alumina refractory castables enriched with ZrO₂ or SiC are preferred. If a brick lining is used instead, high-alumina bricks with strong abrasion and thermal-shock resistance should be considered.
In this zone, temperatures exceed 1000 °C—and at the burner locations can reach as high as 1200 °C. It is one of the most demanding service areas for refractories in the entire cement plant. The process conditions—typically involving 100 % alternative fuels—subject the lining to aggressive alkali attack. Both castables and bricks used here should be high-alumina grades enriched with additives (such as zirconia or silicon carbide) to enhance resistance to chemical attack and abrasion.
In this zone, temperatures remain high—around 1000 °C. The primary risk, however, comes from alkalis formed during the calcination process in the zone above. Here, low-cement and cement-free high-alumina castables are used. For brick linings, high-alumina bricks with silicon-carbide additives are recommended. The lining often becomes coated with chemical accretions derived from alternative fuels—so severe that they must be removed with air or water during routine maintenance. The refractory must also resist mechanical impact, as chunks of accretion falling from the upper zones strike the inclined surface of the constriction at the bottom of the calciner.
What can we help with?
If you would like to receive free advice or inquire about the selection of refractory linings, leave us your contact details, and we will call you!
Send an inquiryHow to select the gunning mix that resists abrasion from calcined clinker and CO₂ corrosion?
Which refractory type best maintains lining stability during frequent on/off cycles?
How to design the lining and burner positioning to prevent hot spots?
Tertiary Air Duct (TAD)
In the third‐air duct (TAD), where temperatures range from 1000 °C in the hot zone down to 600 °C in the cold zone, operating conditions are challenging. This duct delivers an additional air stream to the process, which not only improves combustion efficiency but also allows precise control of the furnace’s internal temperature. To ensure optimal process performance, key parameters—such as airflow rate, temperature, and pressure—can be dynamically adjusted using advanced monitoring and control systems.
Scope of offer: Lining design Refractory products supply Lining installation services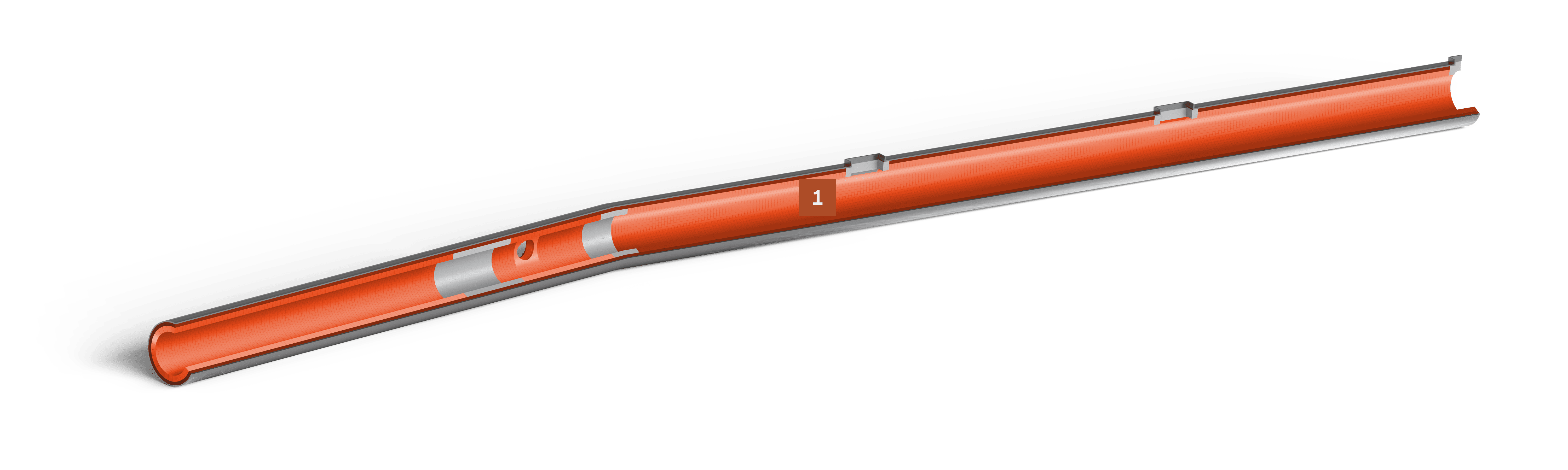
The challenge for the refractory lining in the tertiary air duct lies in its small diameter, which amplifies the effects of the abrasive environment—particles pass through the pipe at high velocity under pressure. To enhance durability, PCO recommends using EXTRATON shaped bricks and chamotte PCOCAST castable with abrasion‐resistant additives such as silicon carbide or zircon. For even harsher operating conditions—higher pressures or temperatures—chamotte bricks with silicon‐carbide reinforcement from the ABRAL line are advised.
What can we help with?
If you would like to receive free advice or inquire about the selection of refractory linings, leave us your contact details, and we will call you!
Send an inquiryHow to select the thickness of insulation to keep the outer shell below target temperature (e.g. below 200 °C)?
What mortar will help to prevent hot‐face brick loosening under cyclic airflow pressure?
How to improve the lining durability at the channel bends?
Riser duct and inlet chamber
The riser duct and inlet chamber are cement‐plant components responsible for conveying the preheated material from the cyclones into the rotary kiln for further heating. Operating temperatures range from approximately 500 °C at the top of the riser to 1100 °C at the transition into the rotary kiln. In addition, the inlet chamber (also called the flue‐gas chamber) collects hot kiln exhaust and routes it back to the cyclone system, enabling heat recirculation. The refractory lining faces several risks: aggressive flue gases (alkali attack), mechanical shocks, and abrasion from the moving charge—issues that are exacerbated in installations equipped with a calciner and a higher proportion of alternative fuels. Therefore, the lining must have low porosity and high wear resistance. PCO Żarów delivers turnkey solutions—from design through installation—providing refractory bricks and castables with Al₂O₃ contents ranging from 30 % to 60 %, enhanced with additives that improve resistance to chemical attack and abrasion.
Scope of offer: Lining design Refractory products supply Lining installation services
In the upper section of the riser duct, where temperatures do not exceed 700 °C, chamotte refractories are used for the working layer. PCO Żarów recommends EXTRATON or ABRAL products, which offer enhanced abrasion resistance. Under more severe conditions, this zone can also be lined with high-alumina bauxite bricks—BAUXITEX—to provide additional protection.
In the lower section of the riser duct, where operating conditions are more severe, the lining must withstand higher temperatures—up to 1100 °C—and intensive chemical attack. Typically, high-alumina refractories based on andalusite or bauxite raw materials are used here, enhanced with additives to boost both mechanical and chemical resistance. PCO Żarów recommends ABRAL or ANDALUX grade products, or ultra-low-cement castables such as NxGel, specifically designed for rapid heat-up processes, to ensure optimal protection of the lining in this demanding zone.
The inlet chamber (flue‐gas chamber) is where the lining is primarily subjected to chemical attack from hot exhaust gases and mechanical impact as the charge falls from the riser duct into the chamber before being fed into the rotary kiln. This causes significant abrasion of the ceramic lining. A common issue is accretion build-up from the feed material, leading to local blockages. The refractory lining should include silicon‐carbide or zirconia additives to enhance resistance to mechanical impact and prevent sticking (imparting low porosity and non-wettability to the bricks and castables). This minimizes accretion formation and allows the lime fines to flow freely into the rotary kiln.
What can we help with?
If you would like to receive free advice or inquire about the selection of refractory linings, leave us your contact details, and we will call you!
Send an inquiryWhich material will improve the lining resistance to chemical condensation products?
How do we mitigate erosion at the riser-to-chamber transition where flow velocity peaks?
What type of refractory will endure the thermal shock without forming gaps on joints?
Main burner
In this zone, where temperatures can exceed 1500 °C, the refractory lining is exposed to rapid heat fluctuations, radiant heat, and attack by oxidizers and sulfur compounds, requiring materials with exceptional chemical‐corrosion and thermal‐shock resistance. The burner’s ceramic lining not only protects the steel structure from degradation but also manages heat flow effectively, minimizing thermal losses and enhancing combustion efficiency. In this area, the lining is relined relatively frequently—typically every few months up to a maximum of one year.
Scope of offer: Lining design Refractory products supply Lining installation services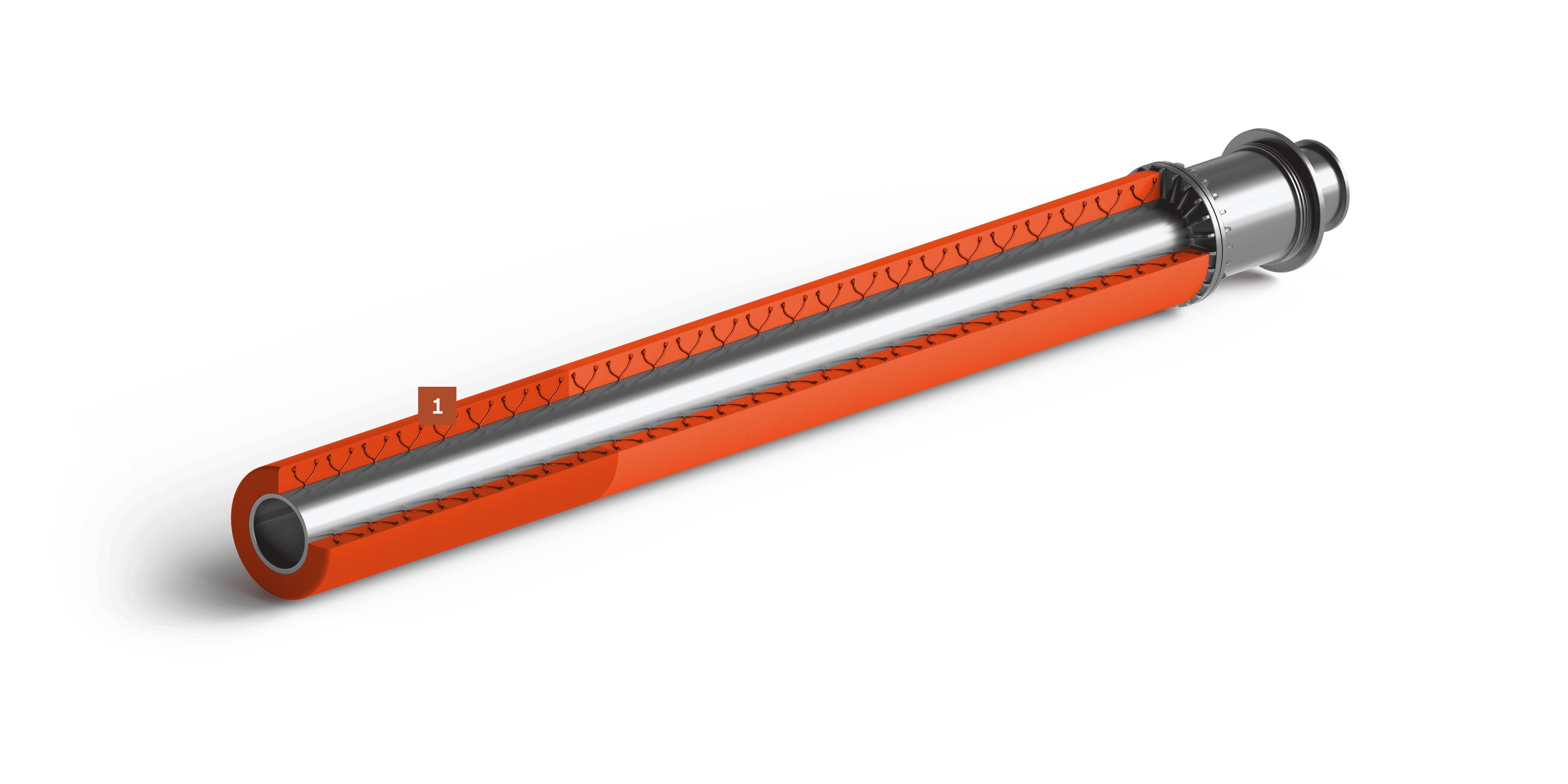
Here, the refractory lining is exposed to very high temperatures and the aggressive action of alternative fuels, necessitating frequent repairs. Installing the lining in the flame zone is challenging, especially when casting concrete directly onto the burner; it requires not only appropriate technology but also highly skilled masons. Achieving a homogeneous concrete consistency is critical to ensure even material distribution and rapid heat-up, which is essential for maintaining uninterrupted furnace operation. Due to these extreme conditions, the refractory material must offer exceptional resistance to thermal shock and aggressive fuels.
What can we help with?
If you would like to receive free advice or inquire about the selection of refractory linings, leave us your contact details, and we will call you!
Send an inquiryHow to design the shape of burner prefab blocks to avoid hot-face lining blowout?
How to select the best refractory for heat load in the burner area?
What preventive maintenance schedule best detects refractory thinning before leak‐through?
Cement rotary kiln
The primary role of the rotary kiln in cement clinker production is to heat the raw feed to very high temperatures (1350–1450 °C), causing its calcination and the chemical reactions that form clinker minerals. The key wear mechanisms of the kiln’s refractory lining include abrasion; thermal stresses from both the charge and the burner; mechanical loads from the rotating steel shell; chemical corrosion from contact with the feed, combustion gases, and slags generated when burning alternative fuels; and attack by aggressive chemical species. For rotary kilns, PCO offers a comprehensive range of materials and services. Our portfolio includes high-alumina refractories with SiC additives—providing enhanced resistance to chemical corrosion, abrasion, and thermal shock—chemically bonded andalusite products with exceptional durability, and chamotte and high-alumina refractories engineered for superior abrasion and chemical-corrosion resistance.
Scope of offer: Lining design Refractory products supply Lining installation services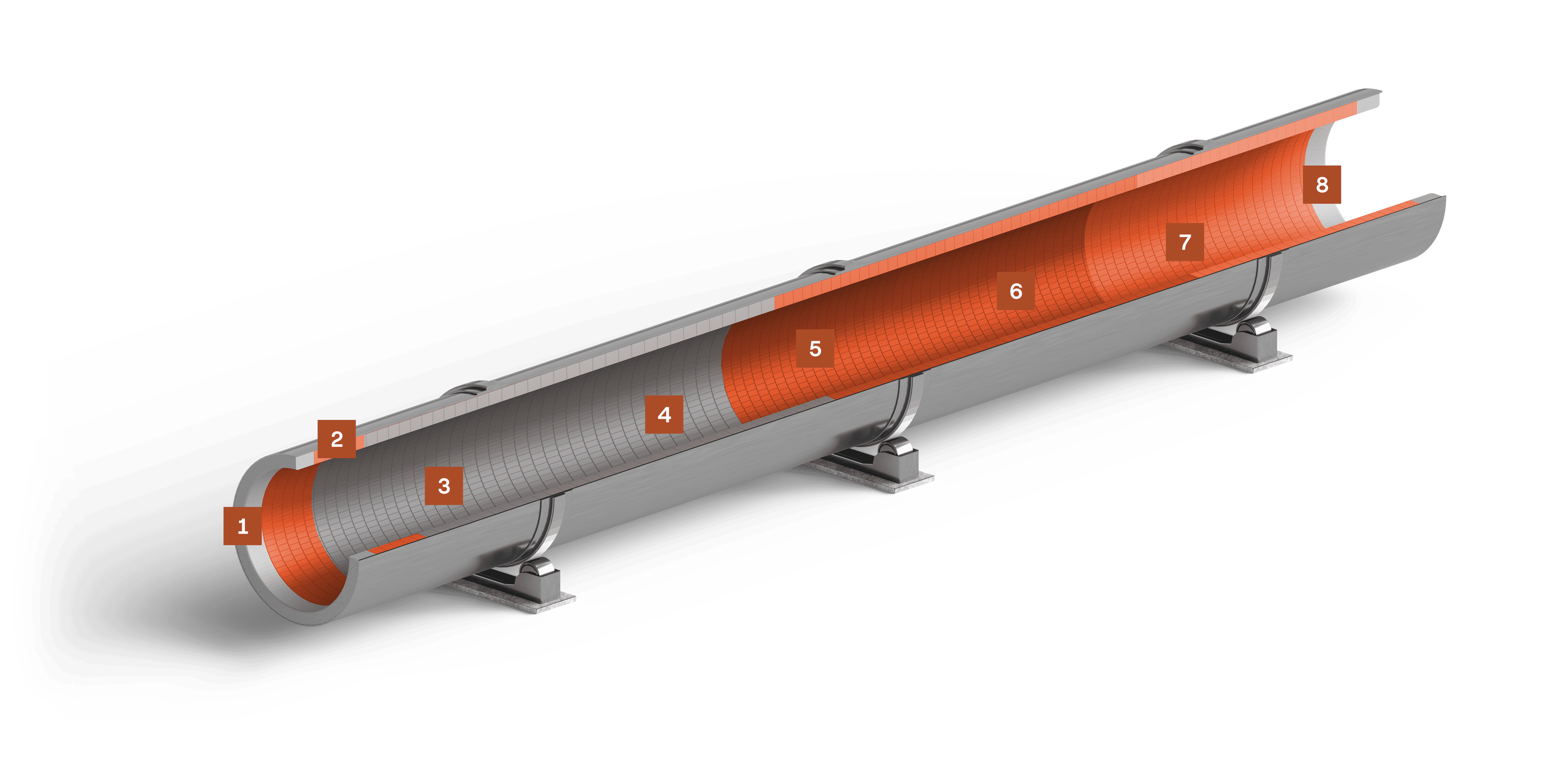
The ending zone of the kiln—known as the “nose ring”—experiences conditions similar to the outlet zone. Here, temperatures fluctuate and the processed charge exerts high mechanical pressure, requiring materials with excellent mechanical strength. The rotary kiln design calls for monolithic products cast in place from refractory concrete during maintenance. The key properties of these materials are compressive strength and abrasion resistance, ensuring structural integrity under intense loading. Recommended products include high-alumina concretes of the MULCAST class and low-cement concretes from the PCOCAST line.
In the cooling zone, the primary challenge for refractory materials is mechanical impact caused by cracking clinker, which changes its volume due to sudden temperature fluctuations. Temperatures in this area vary between 900–1100 °C. The lining consists of a single layer of wedge bricks, and the key properties required of the refractory materials are high resistance to thermal shock and exceptional mechanical strength against impact and abrasion.
In the lower transition zone, the clinker sintered in the previous zone gradually cools down, with temperatures dropping to around 1200 °C. Despite the reduced temperature, refractories with high resistance to dynamic temperature changes are still used. At this stage, magnesite–spinel products predominate, ensuring continuous lining protection while limiting thermal stresses.
The firing zone is the area of highest temperatures—up to 1500 °C—where complete chemical transformations occur. The limestone charge undergoes intense reactions that form the clinker minerals. In this zone, magnesite refractories are recommended, as their properties provide the necessary resistance to the extreme thermal and chemical conditions encountered during firing.
In the upper transition zone, very intense thermal exposure occurs, with temperatures exceeding 1200 °C. This zone is characterized by unstable and fluctuating conditions, and the lining—made of a single layer of wedges—must resist rapid temperature changes. Magnesium–spinel products are typically used here, while at the boundary leading into the safety zone, top‐grade aluminosilicate refractories are installed to provide optimal protection against thermal shocks.
In the safety zone, temperatures exceed 1000 °C, which promotes the decomposition of limestone. Conditions here are variable and heavily dependent on the process—especially when the share of RDF in the fuel increases. The lining, built as a single layer of wedge bricks, is exposed to alkalis, liquid eutectics, unstable stresses, and aggressive chemical and thermal attack from the charge and alternative fuels. Refractory material selection must be flexible to meet these changing operational conditions. In this zone, high-alumina products with SiC—such as ABRAL or ANDALUX—and chemically bonded BAUXITEX refractories should be used.
In the calcination zone of the rotary kiln, in addition to intense mechanical abrasion caused by the movement of the charge, there is exposure to alkali compounds originating from raw materials and fuels. Temperatures in this part of the kiln are maintained between 1000–1100 °C. The lining consists of a single layer of wedge bricks. The key requirements for refractory materials in this zone are high mechanical strength and corrosion resistance, ensuring uninterrupted system operation under variable process conditions. Depending on the specific conditions, products from the ABRAL group—known for their enhanced corrosion and abrasion resistance—are well suited for this application.
In this zone, which marks the start of the kiln lining, the primary hazard is intense mechanical abrasion caused by the advancing charge. To address this challenge, abrasion-resistant castables are employed. It is essential to use high-alumina concrete; the recommended products are medium-cement MULCAST concretes or cement-free GELCAST concretes, both of which provide the necessary strength and resistance to mechanical wear.
What can we help with?
If you would like to receive free advice or inquire about the selection of refractory linings, leave us your contact details, and we will call you!
Send an inquiryHow do we optimize brick shape and orientation to reduce ring formation and clinker buildup?
Which refractory to use in a rotary kiln burning a high share of RDF?
How to include the irregular kiln steel shell shape in the refractory lining design?
Cooler and Kiln Hood
The cooler and kiln hood are designed to cool the clinker after it exits the rotary kiln. In the hood, temperatures can reach up to 1100 °C, while in the cooler they gradually decline—from approximately 800 °C in the hot zone down to around 100 °C in the cold zone. The cooler comprises a hot zone, a cold zone, a roof, and a bullnose ring. Aluminosilicate refractories are employed throughout all areas of the cooler. Clinker bursts in the hood subject the lining to severe thermal shocks, and abrasion from clinker movement is the primary wear mechanism. Additional threats include thermal cycling and the chemically and mechanically erosive action of process gases. The bullnose ring—located adjacent to both the hottest gases and the clinker—is particularly prone to wear. PCO offers an extensive range of refractories for cooler installations, including refractory castables, prefabricated concrete modules, and bauxite bricks.
Scope of offer: Lining design Refractory products supply Lining installation services
In the hot zone of the cooler, temperatures can reach up to 1000 °C and then drop sharply toward the moving grate. These conditions produce severe thermal shocks, and on the clinker bed the primary threat to the refractory lining is intense mechanical abrasion resulting both from the charge movement and from dynamic flows of air and dust. The lining in this zone is built using precast concrete modules—so-called retaining wall elements—which provide not only effective thermal insulation but also mechanical stability under fluctuating temperatures. A key factor in ensuring reliable performance is the use of high-alumina castable, which offers outstanding resistance to thermal shock and severe abrasion. This ensures the material retains its operational properties even under rapid temperature declines and mechanical stresses.
In the cold zone, thermal conditions are very stable, and temperatures do not exceed 500 °C. Due to the gentler temperature exposure and fewer dynamic changes, this part of the cooler experiences low thermal and mechanical stresses—making relines relatively infrequent. In this zone, the lining is made from shotcrete, which provides a uniform, continuous refractory surface. Additionally, along the grate, prefabricated retaining‐wall modules are installed, using lower‐grade refractories such as MULCAST BN45M S5.
The roof, which spans both the hot and cold zones, is subjected to abrasion from volatile dusts and to rapid temperature fluctuations along the cooler’s entire length. The refractory lining must resist mechanical wear as well as variable thermal stresses. For the roof, it is crucial to use materials with outstanding mechanical and thermal properties—particularly in the hot zone, where the inclusion of SiC additives enhances the lining’s strength. In the cold zones, the priority is maintaining a cohesive, durable lining at lower temperatures, allowing for prolonged service without frequent relining.
The primary function of the kiln hood is to recover the clinker and transfer it into the cooler, all under severe mechanical and thermal stresses. Special attention must be paid to the area known as the bullnose ring—a vertical wall that is most susceptible to damage. In this zone, the refractory lining endures mechanical loads from falling clinker combined with rapid temperature changes, placing extremely high demands on the materials. In the kiln hood, the lining is typically made of shaped refractory bricks that provide thermal stability and sufficient insulation, minimizing heat losses and the influence of external factors. In the bullnose ring, however, the extreme mechanical loads call for high-grade refractory castable or precast concrete modules.
What can we help with?
If you would like to receive free advice or inquire about the selection of refractory linings, leave us your contact details, and we will call you!
Send an inquiryWhich abrasion-resistant castable resists clinker fallout erosion at the bullnose ring?
How do we prevent thermal shock damage during cooler gas‐flow fluctuations?
How to design the prefab retaining walls to secure the lining against vibration from the cooler grate?
Shaft kiln
The shaft kiln used in lime production operates at temperatures often exceeding 1100 °C, and its calcination process requires an even, controlled heat distribution along the kiln’s entire length. Limestone fed into the kiln is mixed with coke or anthracite, and fuel combustion generates the high temperatures needed to convert the stone into quicklime (calcium oxide, CaO). In the soda‐ash industry, lime is produced in kilns that run at somewhat lower temperatures than those used in conventional lime manufacturing, reducing the demands on refractory materials and heating systems. By contrast, the kilns used in sugar mills for lime processing face unique operating conditions, with frequent temperature changes and shutdowns. This necessitates durable refractory materials capable of withstanding cyclic thermal variations without excessive wear. In these kilns, calcination is not continuous, which distinguishes them from those employed in other sectors like lime or soda production. frequent stops and temperature swings accelerate lining wear, so sugar‐mill kilns require refractories with enhanced thermal‐shock resistance.
Scope of offer: Lining design Refractory products supply Lining installation services
The heating zone is the area where limestone mixed with fuel is loaded cyclically. This process generates intense abrasive wear due to the mechanical movement of the charge, while also exposing the lining to high temperatures. Materials used in the heating zone must offer high abrasion resistance—hence the choice of EXTRATON aluminosilicate refractories. To reduce heat losses, an insulating layer based on ISOLUX products combined with mineral wool provides excellent thermal‐insulation performance. The key is to balance mechanical durability with insulating properties to ensure the lining’s longevity while maintaining the kiln’s optimal thermal parameters.
The firing zone—often synonymous with the calcination zone—is where the intense thermal treatment of the charge (such as limestone or dolomite) takes place. The firing temperature and the charge composition dictate the specific chemical and thermal stresses, including the risk of hydration. Under normal operating conditions, alumina (Al₂O₃) and silica (SiO₂) are chemically stable, which limits their reaction with water. However, it remains essential to use refractories that maintain stability even in the presence of moisture. In this zone, it is critical to employ products that offer high resistance to hydration and chemical stability at elevated temperatures. MULITEX, ANDALUX, and BAUXITEX refractories meet these requirements, ensuring long service life despite the variable chemical environment of the charge.
In the cooling zone, the lining is subjected to a gradual reduction in temperature, resulting in less severe thermal stress but still requiring abrasion resistance. In a single‐shaft kiln, uniform cooling occurs along the entire height of this zone, allowing for a consistent insulating approach. For the cooling zone, chamotte refractories perform best, offering good compressive strength and abrasion resistance. In particular, SUPERTON‐grade products are recommended for this area. In single‐shaft kilns, the insulating layer throughout this zone is constructed with ISOLUX modules supplemented by mineral wool, creating a continuous thermal barrier and minimizing heat losses.
What can we help with?
If you would like to receive free advice or inquire about the selection of refractory linings, leave us your contact details, and we will call you!
Send an inquiryWhich high alumina bricks best resist the chemical degradation from prolonged CO₂ exposure in the shaft atmosphere?
What gunning mixes or ramming masses offer optimal resistance to repeated slaking and steam attack from the wet lime feed?
How should brick shape, steel anchor design and joint configuration be optimized in a tall shaft geometry to accommodate axial thermal expansion and prevent lining collapse?
Maerz kiln
The Maerz furnace, used in processes requiring precise temperature control and uniform heat distribution, operates under conditions where the ceramic refractory linings are exposed to very high temperatures, often exceeding 1200 °C. A distinguishing feature of Maerz furnaces is the principle of reversal, which sets them apart from other shaft kilns. Two shafts are used: one for calcining limestone and the other for supplying combustion air. Reversal means that the firing and calcination processes alternate in reverse order—first combustion, then calcination—allowing more effective temperature control and improved energy utilization by managing the gas flow in alternating phases. Because Maerz furnaces achieve higher throughput and face more demanding operating conditions, they require refractories of superior quality compared to conventional shaft kilns. These materials must offer exceptional resistance to thermal shock and chemical erosion to maintain lining integrity under changing conditions. Optimizing heat distribution and minimizing thermal losses are therefore critical for the efficiency and long‐term performance of the Maerz furnace.
Scope of offer: Lining design Refractory products supply Lining installation services
The heating zone in a Maerz furnace extends from the lower burner level to the upper part of the shaft, where limestone mixed with fuel is loaded cyclically. This process generates intense abrasive and thermal stresses due to the direct contact between the charge and the lining, as well as fluctuating temperature conditions. Therefore, in this zone it is critical to provide materials with high abrasion resistance and to minimize heat losses, which in turn maximizes the efficiency of the entire furnace. The lining design in the heating zone is based on using different materials selected according to the temperature profile. In the lower section around the burners, the working layer is made of magnesite–spinel refractories, which offer high abrasion resistance and withstand the aggressive compounds formed during combustion. In the upper part of the shaft, high‐abrasion aluminosilicate products from the EXTRATON line are employed.
To ensure a smooth transition between the magnesite–spinel layer and the aluminosilicate layer, a transitional lining made of high-alumina (andalusite) refractories is introduced. Additionally, the space between the steel shell and the working lining is filled with an insulation system that includes ISOLUX insulating boards and mineral-wool insulation blankets. In some designs, an extra insulating layer of SUPERTON or EXTRATON products is placed between the working layer and the main insulation system. The entire shaft lining is finished with a conventional castable layer, providing the final protection and sealing of the structure.
The firing zone extends from the lower level of the supporting arches up to the lower level of the burners (gas lances). In this part of the kiln, the charge undergoes an intensive firing process that generates both very high temperatures and aggressive chemical conditions, depending on the type of raw material—such as limestone or dolomite. PCO Żarów supplies the protective and insulating materials for this zone. The entire lining of the shaft, from the expansion‐joint area upward, is built using specialized shapes—types AS1, AS2, and similar—manufactured from MULITEX or ANDALUX refractories. This approach ensures not only structural stability but also reliable performance under fluctuating firing conditions.
In the Maerz furnace construction, there are elements such as columns, inter-column arches, flat arches, and the connecting duct, all made from low-cement or cement-free castables. Building the columns in a Maerz furnace requires a combination of so-called nose-shaped blocks (VK-76x and WL-76), which ensure exceptional structural stability. In a pillar-less Maerz furnace, the base of the suspended cylinder is also made from high-strength castables, and the flat arch is lined with an insulating layer of lightweight castables—such as ISOCAST or ISOGUN—supplemented with mineral wool.
The cooling zone in a Maerz furnace extends from the level of the first refractory lining down to the lower level of the inter-column arches. In this section, the temperature gradually decreases, which is critical for stabilizing the cooling process. Despite the drop in heat, the lining remains subject to intense abrasive and mechanical stresses caused both by the movement of the charge and by the thermal-stress cycles generated during cooling. The working layer is made from chamotte refractories – SUPERTON or EXTRATON series are recommended, as they perform exceptionally well under these conditions. The inter-column space is typically lined with EXTRATON shapes. The insulating layer in the cooling zone is based on ISOLUX modules, installed in combination with calcium-silicate boards and mineral-wool blankets to complete the thermal barrier.
What can we help with?
If you would like to receive free advice or inquire about the selection of refractory linings, leave us your contact details, and we will call you!
Send an inquiryHow does pillar‐brick design matter when considering the compressive load strength of the lining?
Which refractory grade survives the combined abrasive and chemical wear of limestone calcination?
How to design the lining backup and transition areas to accommodate for the lining expansion/contraction at cyclic heat-up and cool-down?
Rotary kiln for production of lime and pulp
The rotary lime kiln used in the Kraft process recovers lime from lime slurry for subsequent use in pulp and paper production. Its refractory lining is typically two‐layered to provide both durability and resistance to the extreme operating conditions. The greatest threats to the lining are rapid temperature fluctuations, chemical attack by the lime slurry, and the pressure and stress cycles induced by the kiln’s rotation. Different refractories are employed in each kiln zone. At the inlet and outlet, castables with high resistance to both thermal shock and chemical corrosion are used, alongside chamotte and andalusite bricks. In the firing zone, andalusite bricks enhanced with P₂O₅ are most common; these guarantee resilience to extreme temperatures, aggressive chemicals, and deliver high mechanical strength.
Scope of offer: Lining design Refractory products supply Lining installation services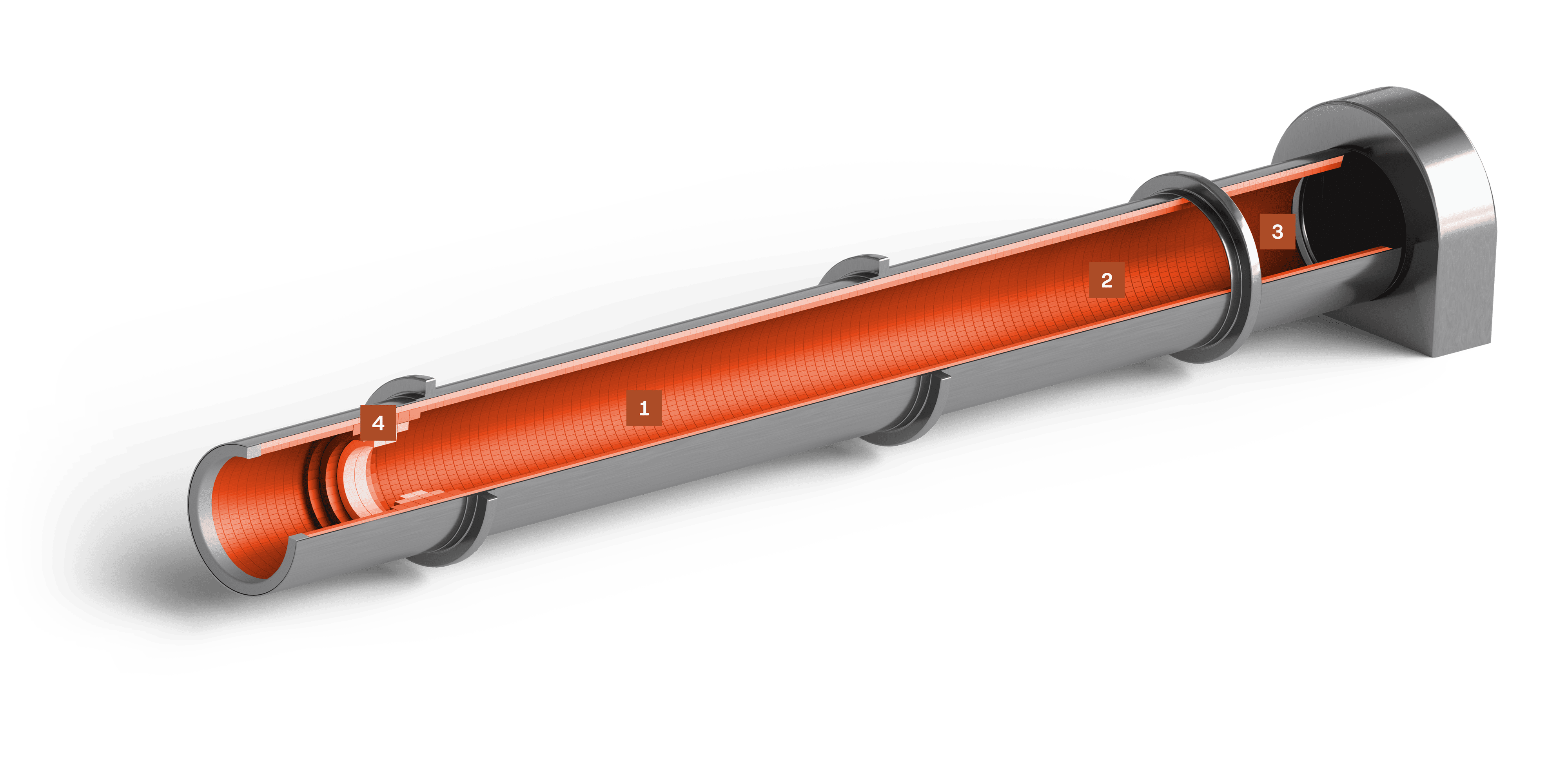
The heating zone of the rotary lime kiln covers the temperature rise from 200 °C to 1100 °C. Here, the slurry is dried and initially calcined. The refractory lining is subjected to abrasion and chemical erosion. The slurry contains alkali salts, sulfur compounds, and chlorides, which pose a risk of chemical infiltration into the lining. Another hazard is that the slurry can be wet (up to 20 % moisture), so the refractory must resist water penetration into its pores. For the working lining, high-grade chamotte refractories with low porosity and alkali resistance—such as EXTRATON—are recommended. In the section closer to the firing zone, where temperatures are higher, high-alumina or chemically bonded refractories—such as ANDALUX—should be considered.
Temperatures in this zone range from 1100 °C to 1300 °C along its entire length. Operating conditions here are variable; the main risks are thermal stresses from the burner flame and chemical attack by the process gases. The lime slurry is sintered, converting the carbonate-bearing mud into pure CaO (quicklime). The refractory lining must resist thermal shock, sustained high temperatures, and both chemical and mechanical corrosion. The lining is two-layered; for the working layer in this zone, chemically bonded andalusite bricks of the ANDALUX grade are recommended.
This is the shortest section of the rotary kiln and spans a few meters before the inlet to the cooler. Here, temperatures drop rapidly—from 1000 °C to around 200 °C—creating severe thermal shocks. At this point, the fully reacted lime acts abrasively on the lining as it moves with the charge. The kiln’s rotation and the converging construction (reduced shell diameter) impose mechanical stresses that are hazardous to the refractory. The lining is two-layered: at the constrictions, a high-alumina refractory castable is used for the working layer, while the insulating layer employs ISOLUX shaped boards with enhanced compressive strength.
The charging threshold is made of refractory ceramic and is designed to even out the distribution of the charge at the rotary kiln outlet. In this zone, the lining is subject to significant abrasion and mechanical stress. The recommended installation uses the most durable andalusite bricks, which help regulate the movement of the charge.
What can we help with?
If you would like to receive free advice or inquire about the selection of refractory linings, leave us your contact details, and we will call you!
Send an inquiryWhat refractory type to consider against tar and organic acid corrosion on the hot face?
How can we prevent lining damage from differential expansion between the shell, the insulating layer and the hot face layer of bricks?
How to track the refractory wear loss in areas under the influence of sludge or in the burner area?
Why choose PCO?
Installation service together with refractory supply – easier project management and a single guarantor of quality
Complete range of aluminosilicate refractories for the cement, lime and paper industries
Own team of designers and engineers ready to aid with any task
Selected Products and Services for the Coke Industry

ABRAL Product Line

Ultra‐Low‐Cement refractory Castables (ULCC)
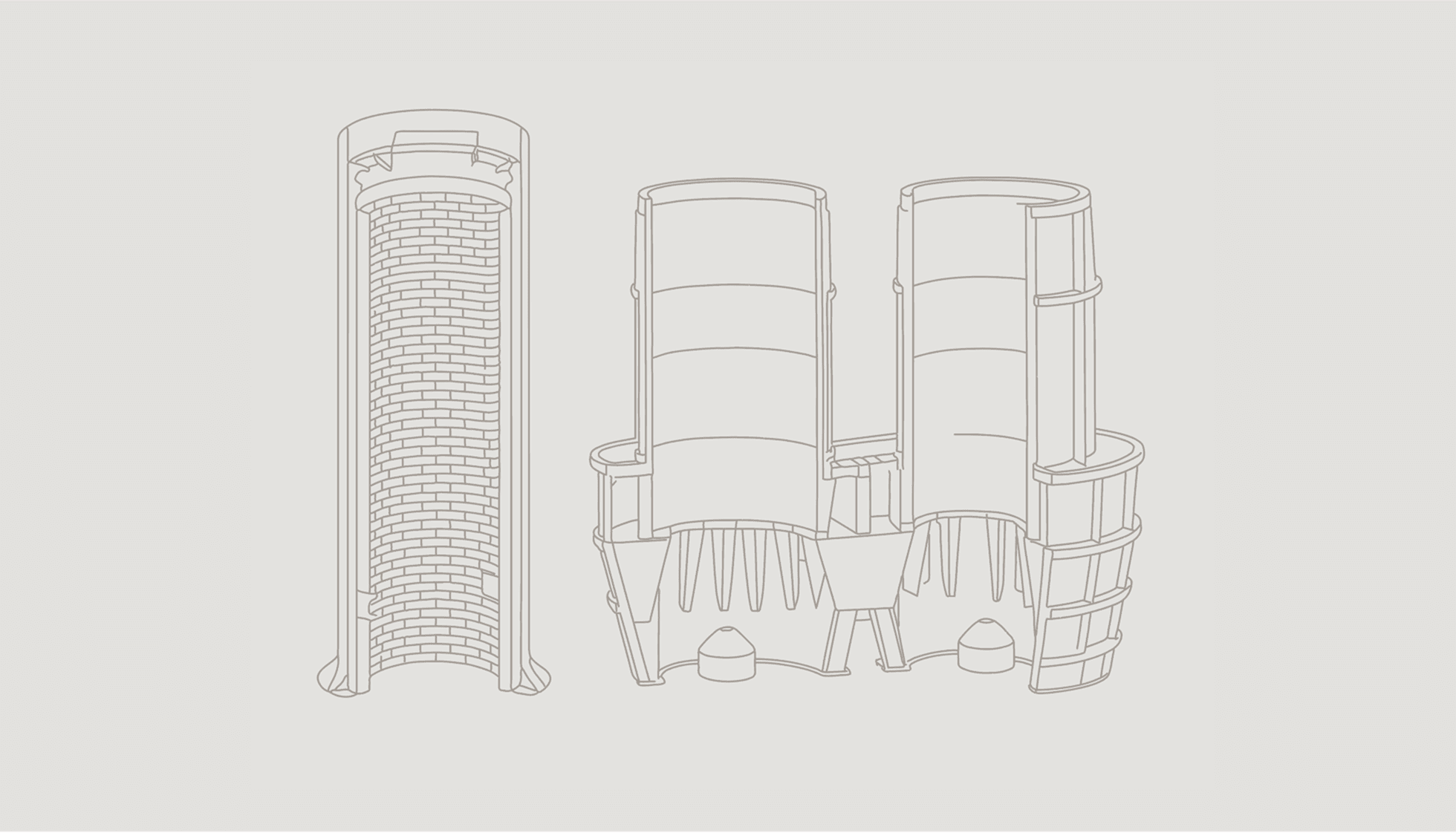
Supervision of shaft kiln and Maerz kiln relining projects
Contact us
Please select the option that best describes the subject you want to discuss with us. This will help us direct your inquiry to the right person at PCO.