Refractory precast elements
Our portfolio of refractory materials
Refractory monolithic precast shapes offer a solution that eliminates the need to cast concrete on the construction site.
These products have two key advantages: they accelerate the assembly process of the lining and ensure proper thermal treatment of the concrete before the furnace startup (dried by the manufacturer before shipment). Refractory concrete prefabricates are produced in a dedicated process and delivered to clients as ready-to-install elements, eliminating the need to halt refurbishment works for concrete setting and drying times and alleviating concerns about the drying process of the lining. Performing the forming and drying process at the manufacturer's facility enables achieving the highest resistance to temperature and thermal shocks, as well as resistance to structural degradation and the action of aggressive chemical agents during the lining's operation
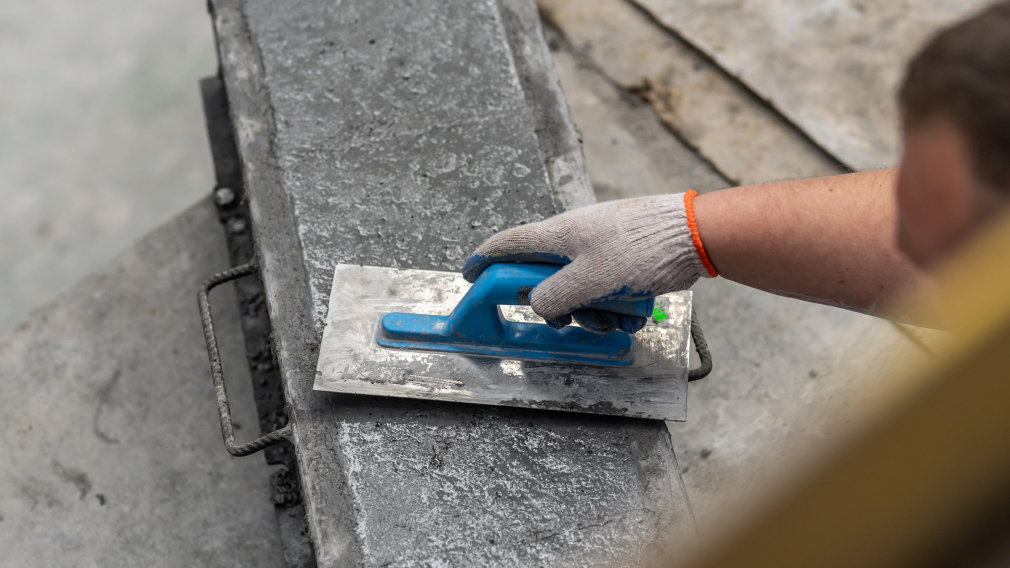
Shapes
Nadajemy prefabrykatom dowolny kształt
As a manufacturer of monolithic precast shapes, we have introduced prefabricates to our product portfolio to provide customers with ready-to-install refractory concretes, eliminating the need for further thermal processing, which can be time-consuming and difficult to carry out on-site during refurbishment.
Our team of designers is available to help develop the optimal shape of the product, select the appropriate grade of concrete for the working conditions of the prefabricate, and consider the use of special internal reinforcement or a transport system to facilitate product installation.
The largest formats we produce are single-piece, high-temperature resistant concrete prefabricates with a weight exceeding 7 tons and maximum dimensions of 4200 cm.
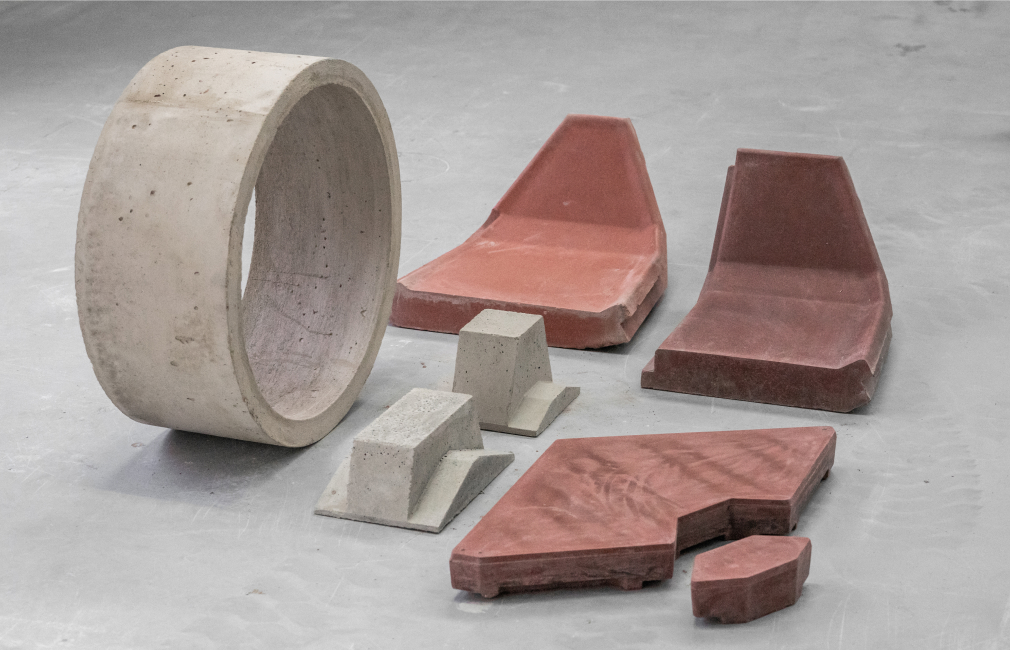
Why choose our products
Flexible production department
We specialize in designing and producing precast shapes of various sizes, ranging from small to several meters in formats, in series from a few to several hundred pieces. The composition of the concrete mix and the curing time are carefully adjusted to achieve optimal parameters of the final product, regardless of the complexity of the shape.
Drying of prefab elements
The cast shapes can be pre-cured at temperatures up to 650 °C. The drying process occurs both in a dedicated dryer and in an oven, ensuring the final product has excellent utility properties, is ready for installation, and has a safe startup of the lining.
Precast shape design service
We will plan the shapes and their installation method to match the lining design perfectly. Our clients can save time casting and drying concrete in hard-to-reach areas of the lining. Ready-made concrete prefabricates are easy to install and similar to brick.
Own steel mold workshop
We recommend using metal or plastic molds. They provide greater dimensional accuracy than traditional wooden molds and show less wear during the production of more extensive series. We manufacture molds in our workshop, considering the behavior of concrete during the drying process (permanent dimensional change of the product).
Embedding steel elements
Where the working conditions of the prefabricate allow, we can embed reinforcing/fixing elements made of high-temperature steel or apply dispersed reinforcement, which increases the element's resistance to mechanical loads.
Dedicated concrete production process
We manufacture prefabricates in a process dedicated to a specific type of refractory concrete. This means selecting the appropriate mass composition, aggregate granulation, and controlled casting and drying. The production process varies depending on the binding system used in the material (cement, chemical additives, hybrid systems).
Production process and quality control steps
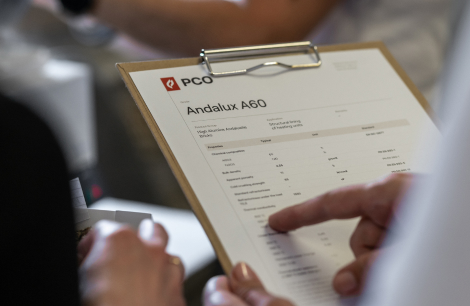
We control the quality of every delivered batch
Quality tests of each production batch are conducted in our fully equipped laboratory. These include checks of chemical composition, density, porosity, temperature resistance, expansibility, and thermal conductivity, which ensures the consistently high quality of our products.
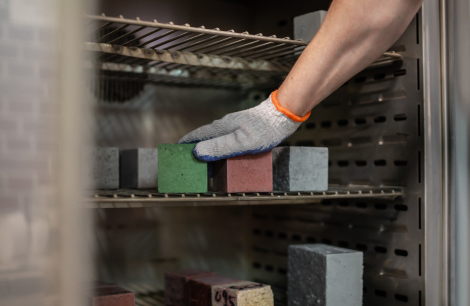
Transparent technical specification of products
Our Technical Data Sheets include a column with the product’s guaranteed properties. A dedicated Standard Tolerances document applies for each family of formed refractory products, clearly defining the quality framework without surprises.
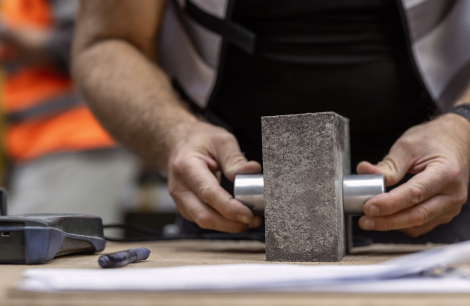
We issue international inspection certificates
We test and report product values according to commonly used industry standards, such as ISO and ASTM. Each order is documented with a type 3.1 certificate by the EN 10204 standard, available in selected languages.
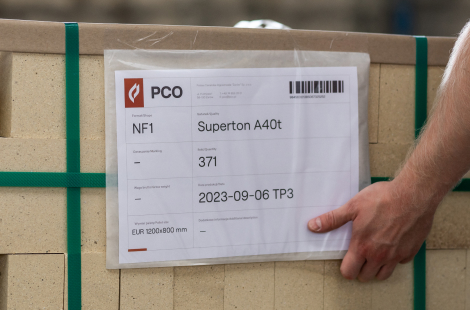
Insight into the production history of each product
All processes in our factory comply with the ISO 9001 management standard. An integrated ERP and workflow management system records every stage of production. Using barcodes, we have complete insight into each product’s history, enabling precise tracking of when and from which batch of raw material was produced.
Supplementary products
In addition to refractory ceramics for the working layer of linings, we also provide a range of additional products.
Do you need help deciding which material to choose or how to arrange the brick layers? Our engineers will perform a temperature flow calculation for you and suggest a layout from the working layer to the insulation layer.
Refractory mortars heatseting and airsetting, ready to use
Ceramic papers, thicknesses 1 to 5 mm
Bulk ceramic fiber, ropes and sealing joints
Semi dense insulating boards, thicknesses 10 to 100 mm
Calcium-Silicate boards
Ceramic fiber blankets, thicknesses 13 to 100 mm
Our offer
Contact us
Please select the option that best describes the subject you want to discuss with us. This will help us direct your inquiry to the right person at PCO.