Quality, occupational health and safety and corporate social responsibility
Quality management
Our quality management system is based on the ISO 9001 standard, guaranteeing clients that all processes in our factory are organized and controlled according to international standards.
We record production data, providing complete and up-to-date information on the history of each order.
All processes, from sales organization to product quality control, are annually validated by external control entities.
We believe that one of the key characteristics of refractory materials should be their reliability. Therefore, we have designed a comprehensive system for quality management of our ceramics, based on the best global standards such as the ISO 9001 standard.
The production process of our products is recorded through IT systems (SCADA and ERP), enabling access to complete and current information on the production process.
To ensure the proper maintenance of our quality management system, we validate its functionality annually through audits by an external and independent control entity.
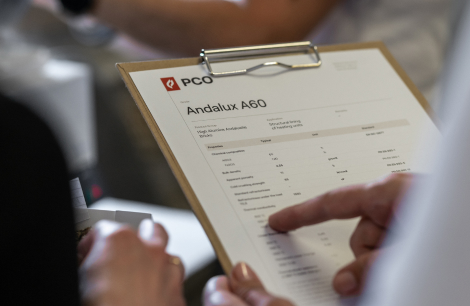
Transparent Technical Specification of Products
We believe that the reliability of our refractory materials is crucial. Therefore, we ensure that our technical documentation leaves no doubts about the properties of the products we deliver. For each family of shaped products, a dedicated Standard Tolerance document is in place, according to which we control product compliance with general quality standards. Each of our Technical Data Sheets includes a column with the typical guaranteed properties of the product.
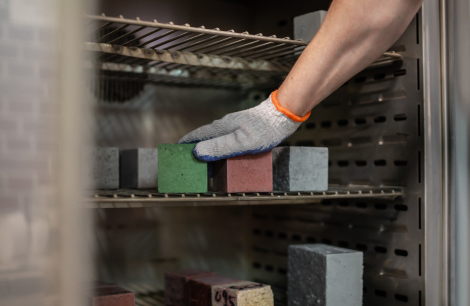
Quality Control of Every Delivered Batch
Our products must be reliable from the first brick to the last one we deliver. To ensure this, we conduct property tests for each production batch in our own laboratory. Our experienced Technicians and Lab Assistants use available equipment to test the most important properties of our materials: chemical composition, density and porosity, compressive and flexural strength, abrasion resistance, and refractoriness under load.
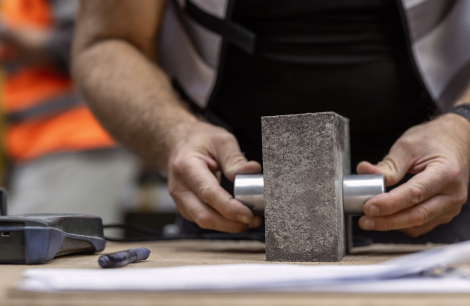
Issuing Internationally Recognized Control Certificates
We understand that proper documentation is the foundation of an efficient quality management system. The property tests we conduct are carried out according to international standards, ensuring an objective assessment of our products' quality. For each produced batch, we can issue a quality certificate in compliance with EN 10204 in any language chosen by the client.
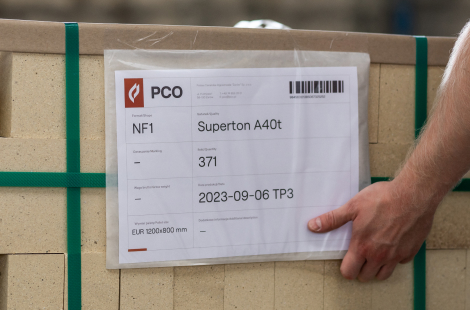
Insight into the Production History of Each Product
Effective quality management requires a lot of data. To collect and analyze it correctly, we use our SCADA and ERP systems. During production, unique identifiers are assigned to production batches, which can be read using a barcode. This provides quick and easy access to information about each semi-product and product—what raw material batches it came from, on which equipment it was made, and by whom. Such precise information allows us to manage and eliminate non-conformities identified by our Quality Department accurately.
Quality Control Points
Our quality control system includes specific actions at each stage of production. These actions are tailored to the type of product and its process, and we categorize them into: control of dense products, insulating products, concretes and mortars, and concrete prefabricates.
Detailed guidelines for actions such as sampling plans, types and conditions of tests conducted, and methods of reporting non-conformities are entirely based on the requirements of the ISO 9001:2015 standard.
A description of the quality control points can be found on the Product category pages.
Dense refractory firebricks | Insulating refractory firebricks
- Preparation of raw material mix
- Production of molds
- Molding
- Firing
- Finishing
- Packing
Refractory castables, masses, and mortars
- Preparation of the dry mix
- Packing the mix into bags
- Palletizing and wrapping
Refractory precast shapes
- Preparation of the dry mix
- Preparation of the wet mix (concrete)
- Mold preparation and concrete casting
- Drying at temperatures up to 600 °C
- Finishing
- Packing
Occupational Health and Safety
The attention to detail we apply in producing our high-temperature resistant products is equally important in the context of our health and safety standards for our team.
We have precise safety procedures and standards that not only protect our employees but also ensure the safety of subcontractors from potential exposure to hazardous situations.
Safety First
Our priority is to achieve a zero incidence rate of occupational diseases and accidents. Our team is our greatest asset, and their health and safety are paramount to us. We encourage our employees to perform tasks thoroughly and to halt operations if safety conditions do not meet our standards and protocols (pit stop meetings).
Risk Minimization
We ensure that workstations are organized in an ergonomic and safe manner. Automated production stations are equipped with photocell systems, and employees use a complete set of personal protective equipment tailored to the work environment. We regularly measure risk factors, and if any non-compliance is detected, we immediately implement appropriate corrective actions.
Prevention and Awareness Raising
We take a serious approach to awareness, prevention, and continuous improvement. Every employee gains knowledge about safely performing their tasks through participation in training and using workplace instructions. Daily, in each department, internal OHS inspectors and duty officers, selected and trained from among the employees, are responsible for maintaining high safety standards. We regularly conduct internal OHS inspections, and the reports from these inspections help department managers better and more safely organize work.
Sustainable Development, Environmental Protection, and Corporate Social Responsibility
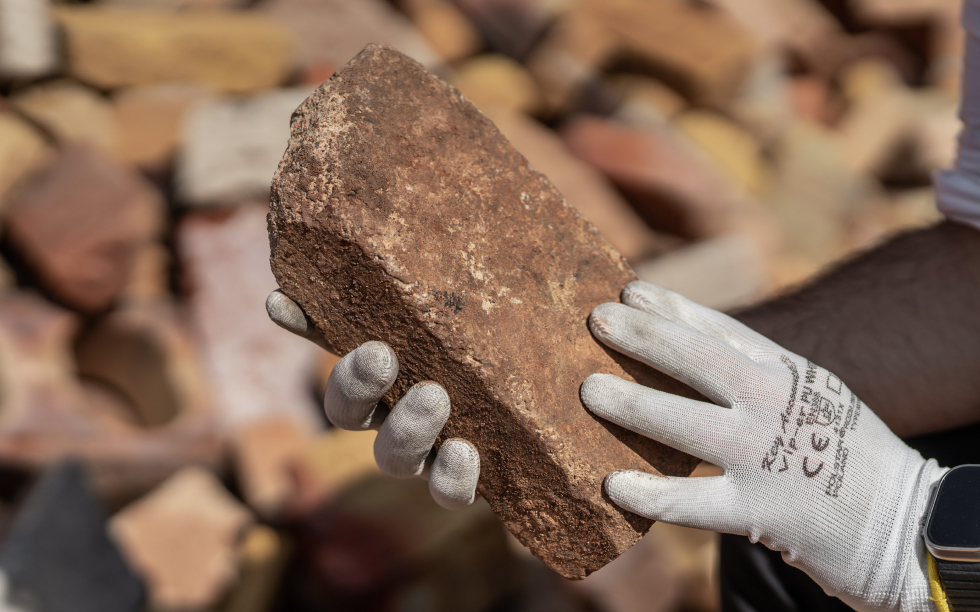
Recycling of Products
We take minimizing the environmental impact of our production processes very seriously. Our goal is to achieve the highest technologically acceptable share of recycled raw materials from the demolition of industrial furnaces. This approach ensures a closed loop that minimizes waste and reduces greenhouse gas emissions (from raw material production processes) and limits the use of natural resources.
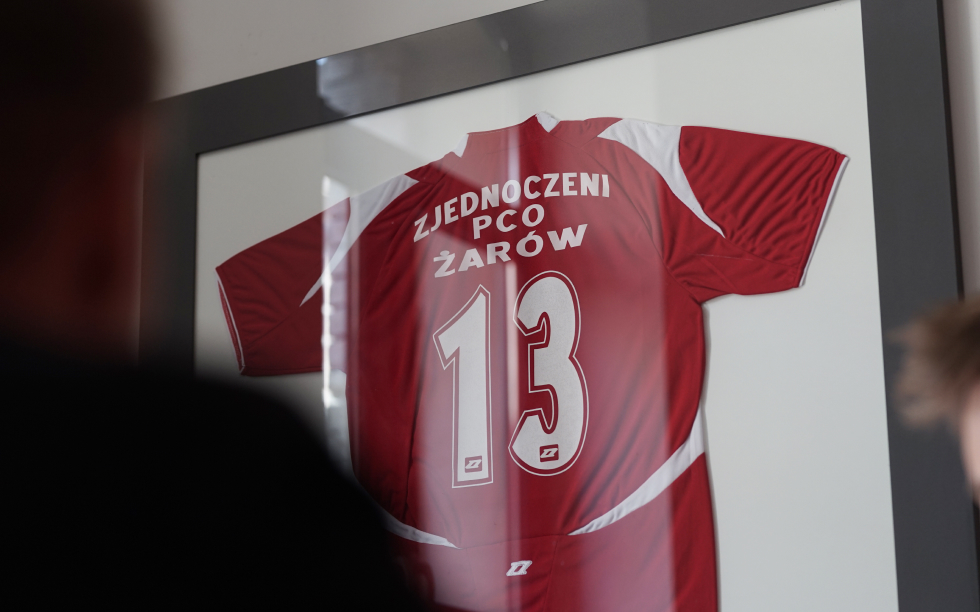
Success Through People
From the very beginning, our refractory materials factory has played a key role in the local job market. People from Żarów, who have been the backbone of PCO’s workforce for generations, have contributed to the company's development, which in turn has led to the economic growth of the Żarów municipality. Each year, we allocate funds to support social initiatives organized by the City Hall and support projects by local foundations, artists, activists, and history enthusiasts of the Żarów municipality. Additionally, we sponsor the KS Zjednoczeni Żarów football team and support the activities of the Volunteer Fire Brigades in Żarów and Mrowiny. In recent years, it has become a tradition for our employees to participate in collecting donations for needy families as part of the annual "Noble Package" campaign. Our success is the result of the involvement of the entire community.
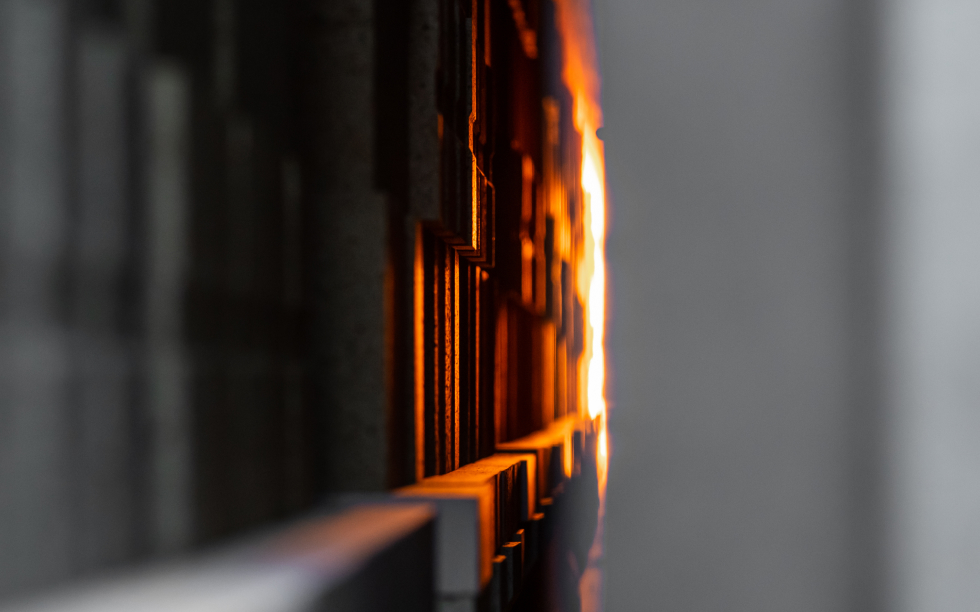
Green Energy
We consistently use energy recuperation from the firing process. The recovered heat is used for heating utility water and rooms. Additionally, by using a generator, we convert waste heat into electricity. We also generate electricity using industrial photovoltaic panels installed on the plant premises. We are gradually replacing our fleet of forklifts with electric models, which will reduce greenhouse gas emissions from this source.
Contact us
Please select the option that best describes the subject you want to discuss with us. This will help us direct your inquiry to the right person at PCO.