Who we are
Refractory materials manufacturer
We are a Polish manufacturer of refractory ceramics and specialists in delivering comprehensive refractory solutions.
Our refractory manufacturing team consists of over 200 professionals in technology, engineering, and the production of aluminosilicate products.
The company's headquarters and production plant are located in Żarów, Poland, at the heart of continental Europe. We supply over 60,000 tons of refractory products yearly in over 180 unique varieties.
Our product portfolio includes refractory materials, such as refractory bricks, shapes, concrete, and insulating materials. We complement our product range with design and installation services for ceramic linings.
Our comprehensive approach allows us to deliver turnkey solutions, from the technical concept of the installation through the supply of necessary materials to execution.
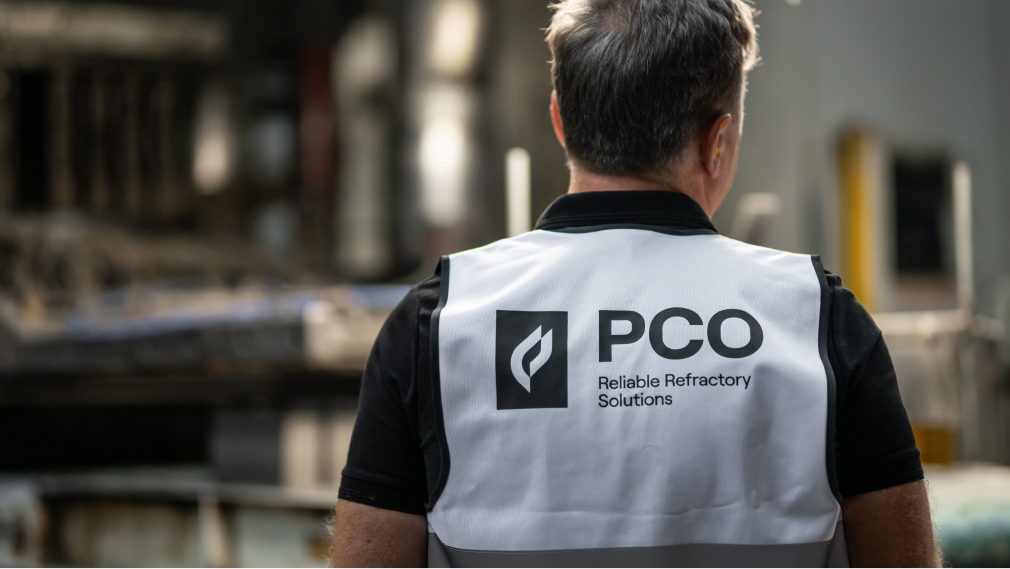
Key facts & figures
Production facility and resources
Our offer
Where are we located
Contact us
Please select the option that best describes the subject you want to discuss with us. This will help us direct your inquiry to the right person at PCO.